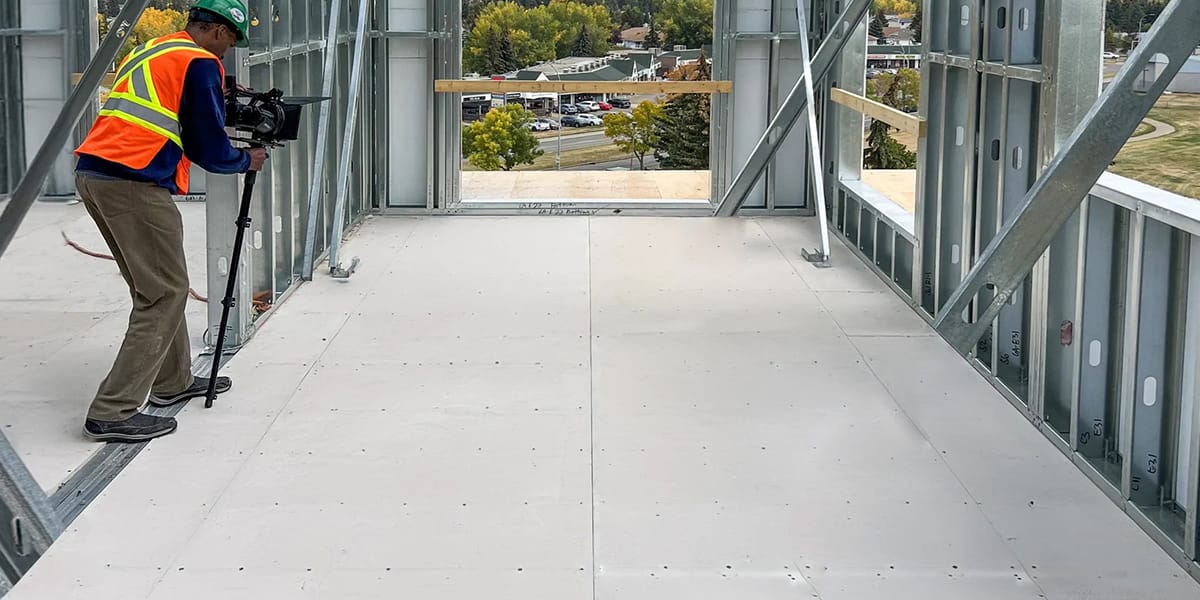
24 Jul Water Resistant Subfloor Materials Compared for Modern Homes
Table of Contents
- 1 Key Takeaways
- 2 Subfloor Basics
- 3 Water Resistant Subfloor Options
- 4 Comparison Table
- 5 Material Profiles
- 6 Practical Tips for Subfloor Installation
- 7 Choosing the Best Subfloor
- 8 FAQ
- 8.1 What is the difference between water resistant and waterproof subfloors?
- 8.2 Can you install tile over any water resistant subfloor?
- 8.3 How do you know if your subfloor needs replacing?
- 8.4 Are eco-friendly subfloor materials as strong as regular ones?
- 8.5 How can you protect your subfloor during construction?
You want the best water resistant subfloor options for your home. Modern materials offer many strong choices. Premium OSB is popular in new homes because builders pick it for its ability to fight moisture and last longer. It also comes with warranties against swelling. Other water resistant subfloor options include magnesium oxide panels, cement board, engineered wood, and treated plywood. These materials provide excellent water resistance and strength. Each subfloor option has its own advantages. With growing concern for the environment, you may want to balance performance with its impact on nature.
Key Takeaways
A strong, water resistant subfloor holds up your floors. It stops damage and keeps your home safe and quiet. – Pick subfloor materials by looking at moisture resistance, strength, price, and how they affect the environment. This helps you find what your home needs. – Magnesium oxide panels and cement board protect best from water, fire, and mold. They work well in wet places like bathrooms. – Good installation and regular care help your subfloor last longer. Check for leaks and seal the edges often. – Eco-friendly subfloor choices can be strong and water resistant. They do not hurt the environment.
Subfloor Basics
What Is a Subfloor
You may not see the subfloor in your home, but it plays a vital role in every room. The subfloor sits directly under your finished flooring, such as hardwood, tile, or carpet. It forms the strong, flat base that supports everything above it. Without a solid subfloor, your floors could sag, bounce, or even break under heavy weight.
A subfloor does more than just hold up your furniture and walls. It spreads weight evenly across the floor area, which keeps your home safe and stable. The subfloor also helps reduce noise between floors, making your home quieter and more comfortable. You will find that a good subfloor can even help with energy efficiency by keeping heat in during winter and out during summer.
Common subfloor materials include plywood, OSB, and concrete. Each type offers different benefits, but all aim to provide a stable, flat surface for your finished flooring. The subfloor also acts as a barrier, protecting your floors from moisture and damage. When you choose the right subfloor, you help your floors last longer and look better.
Tip: A strong subfloor extends the life of your finished flooring and keeps your home safe.
Why Water Resistance Matters
Water can cause serious problems for your subfloor. Even a small leak from a dishwasher or washing machine can lead to big issues over time. Here are some common causes of water exposure to subfloors:
1. Leaking appliances or fixtures, such as dishwashers and toilets. 2. Roof or window leaks that let water seep down to the floor. 3. Flooding from storms or plumbing failures. 4. High humidity or poor ventilation, especially in basements and bathrooms. 5. Hidden plumbing leaks under floors or behind walls.
When moisture gets into the subfloor, it can cause rot, mold, and structural damage. Tiles may loosen, and wood can warp or swell. Quick action after water exposure is key to preventing long-term damage. Choosing a water resistant subfloor helps protect your home from these risks and keeps your floors strong for years.
Water Resistant Subfloor Options
When you want water resistant subfloor options, you have many choices. Builders use new materials to stop water from hurting homes. Some of the newest choices are magnesium oxide panels, cement board, engineered wood panels, premium OSB, and waterproofed plywood. These materials help keep your floors safe and strong, even in rooms with lots of water.
New subfloor materials use better core technology. Some products have SPC or WPC cores. These cores have special layers that block water and make the floor stronger. Brands like COREtec, Mohawk, Shaw Floors, Armstrong, and NuCore make subfloors that last longer and stay stable. These products go through hard tests, like soaking in water and being in high humidity. Many new subfloors also have eco-friendly certifications, so you can pick a product that is better for the earth.
Key Comparison Factors
You should compare water resistant subfloor options by looking at some important things:
Moisture Resistance: This shows how well the subfloor keeps water out. Good moisture resistance stops swelling, warping, and mold.
Durability: You want a subfloor that can take heavy use and last many years.
Cost: Think about the price to buy and put in the subfloor and how much you might save on repairs later.
Environmental Impact: Some subfloors use recycled materials or make less pollution. Look for eco-friendly labels like FloorScore or FSC.
Installation Requirements: Some subfloors need special tools or steps, like cleaning, leveling, or adding a moisture barrier.
Maintenance: Easy cleaning and care help your subfloor last longer.
Fire Resistance: Some materials, like magnesium oxide, give extra safety if there is a fire.
Tip: Always check if your subfloor choice has the right certifications for safety and the environment.
Moisture and Durability
You need to think about how each subfloor deals with water over time. Water resistant subfloor options can protect against small spills or damp air. But if water stays on the floor for a long time, some materials may still get damaged. Waterproof subfloors, like those with SPC or cement board, block water completely. These work best in places like bathrooms, basements, or laundry rooms where you expect more water.
Waterproof subfloors stay strong even after being wet for a long time. They do not warp, grow mold, or break down easily. Water resistant subfloors give some protection but may not last as long if they get very wet. You should pick a subfloor based on how much water you expect in each room. For rooms with lots of water, waterproof materials give the best strength and peace of mind.
Comparison Table
When you pick a subfloor, you want to know how each one compares. The table below shows the main features for each material. You can look at moisture resistance, durability, how easy it is to install, cost, lifespan, eco-friendliness, and fire resistance. This makes it easier to choose the best subfloor for your house.
Subfloor Material | Moisture Resistance | Durability | Installation | Cost per Sq. Ft. | Lifespan | Eco-Friendliness | Fire Resistance |
---|---|---|---|---|---|---|---|
Magnesium Oxide Panel | Excellent | Excellent | Moderate | $4–$7 | 30+ years | High | Excellent |
Cement Board | Excellent | Excellent | Hard | $5–$8 | 30+ years | Moderate | Excellent |
Engineered Wood Panel | Good | Good | Easy | $3–$6 | 20–30 years | Moderate | Good |
Very Good | Very Good | Easy | $2.50–$4.50 | 20–30 years | Moderate | Good | |
Waterproofed Plywood | Good | Good | Easy | $2.50–$3.50 | 15–25 years | Moderate | Fair |
Standard Plywood | Fair | Fair | Easy | $2.50–$3.50 | 10–20 years | Moderate | Poor |
OSB | Fair | Fair | Easy | $2.50–$4.50 | 10–20 years | Moderate | Poor |
Note: The cost to install each subfloor can change. For example, premium OSB and plywood usually cost between $2.50 and $4.50 for each square foot. Cement board and magnesium oxide panels cost more because they need special tools and more work. You might pay up to $8 for each square foot for these types. Some brands, like DRIcore and Barricade, sell water-resistant panels for basements and bathrooms. These can cost between $2 and $10 for each square foot.
You can see that magnesium oxide and cement board are best for moisture, lifespan, and fire safety. Premium OSB and engineered wood panels are good if you want a balance of price, easy installation, and good results. If you care most about the environment, magnesium oxide panels are the top choice. Always think about which features are most important for your project.
Material Profiles
Magnesium Oxide Panels
Magnesium oxide panels are a modern subfloor choice. They stop fire, mold, and mildew. These panels are lighter than cement board. This makes them easier to move. You can use them in wet rooms like kitchens and bathrooms. Some panels have a magnesium sulfate binder. This binder helps block water better. You must follow special steps to install them. Use diamond-tipped tools for cutting. Store the panels the right way before using them. The table below shows the main good and bad points:
Aspect | Advantages | Disadvantages |
---|---|---|
Fire Resistance | Excellent fireproof qualities | N/A |
Weight | N/A | |
Resistance | Resists fungus, rot, mildew, allergens, mold | Some types can absorb moisture and swell |
Ease of Use | Lightweight and easy to handle | Needs special tools and skilled installers |
Cost | Energy efficient, durable | Higher cost, quality varies by manufacturer |
Durability | Durable, stable (especially sulfate-based) | Brittle, can crack, weaker nail holding power |
Installation Preparation | Acclimates well if stored properly | Needs careful storage and following directions |
Tip: Always check the binder type. Follow the maker’s instructions for best results.
Cement Board
Cement board works well as a subfloor in wet rooms. You can use it in bathrooms, laundry rooms, or kitchens. It keeps water out and stays strong over time. Cement board does not burn, so it adds fire safety. You must seal it well or it may soak up water after a while. The boards are heavy and need special tools to install. Cement board is better than wood subfloors for water and strength.
Keeps water out and stays strong
Great for wet and humid rooms
Does not burn and handles high heat
Needs sealing and skilled workers
Engineered Wood Panels
Engineered wood panels make a strong and steady subfloor. These panels have layers of wood glued together. They handle normal moisture but should not get soaked. If they get too wet, they can swell or get weak. Special treatments can help them resist water. Always check moisture during storage and when you put them in. Pick the right wood for your area to help them last longer.
Strong and steady for most rooms
Must stay away from lots of water
Premium OSB
Premium OSB is a top subfloor material. It uses more wood fiber and special glue for extra strength. Premium OSB blocks water better than regular OSB. Even after weeks in water, it stays stiff and keeps its shape. You get a strong warranty with premium OSB. This gives you peace of mind. Builders often use this material in new homes.
Dense and strong glue for better water blocking
Comes with strong warranties
Waterproofed Plywood
Waterproofed plywood is a classic subfloor with extra protection. You can use epoxy, waterproof glue, or polyurethane to seal it. These coatings help keep water out, but you must reapply them over time. Always seal the edges and joints for best results. Store plywood in dry places and check for damage often. Marine-grade plywood with waterproof coatings lasts the longest.
Sand and clean the plywood.
Seal all edges and joints.
Check and reapply as needed.
Regular care helps your waterproofed plywood subfloor last longer.
Standard Plywood
Standard plywood is a common subfloor. It costs less and is easy to put in. But it does not block water well. If it gets wet, it can swell, bend, or rot. Plywood dries faster than OSB, which helps stop damage. Use standard plywood only in dry rooms. If you compare plywood and osb, plywood dries faster but is less dense.
OSB
OSB is another popular subfloor. It uses resin glue to block water, but it holds water longer than plywood. When OSB gets wet, it can swell, bend, or grow mold. OSB comes in different grades. Higher grades block water better. Always follow the maker’s rules for putting it in and drying. Good moisture control keeps your OSB subfloor strong.
Holds water longer than plywood
Needs air gaps and good drying
Higher grades block water better
Practical Tips for Subfloor Installation
Installation Advice
You want your subfloor to last and stay strong. Good installation makes a big difference. Before you start, always check the area for damage or moisture. Clean the space well. If you skip this step, your subfloor may not sit flat or could trap water. Use only materials made for subfloors. Particle board does not work because it cannot handle water.
Here are common mistakes to avoid when installing a subfloor:
Not fixing damage or checking for moisture before you start.
Using the wrong materials, like particle board, which does not resist water.
Installing underlayment the wrong way, which lets water get in.
Picking adhesives or fasteners that do not match your subfloor material.
You should always follow the manufacturer’s instructions for installation details. This helps you avoid problems and keeps your subfloor strong. If you need to protect sub-floor from rain during construction, cover it with tarps or plastic sheeting. Quick action keeps water out and helps with protecting sub-flooring.
Tip: Take your time with each step. Careful work now saves you from repairs later.
Maintenance and Repairs
Regular care keeps your subfloor in good shape. You can spot problems early and fix them before they get worse. Use this table to plan your maintenance routine:
Maintenance Task | How Often | What to Look For or Do |
---|---|---|
Check for water stains, mold, or damaged grout | Every month | Look for stains, mold, or peeling paint on floors and walls. |
Inspect grout and caulk | Every 3 months | Find cracks or gaps; reseal if water does not bead up. |
Test exhaust fans | Every 3 months | Make sure fans work to remove moisture after showers. |
Check seals around sinks, showers, and bathtubs | Twice a year | Look for leaks or worn-out seals. |
Inspect paint and wallpaper | Every 3 months | Watch for signs of moisture damage. |
You should also run exhaust fans after showers, open windows, and dry wet surfaces right away. Fix leaks fast to stop water from reaching your subfloor. Keep indoor humidity between 40% and 50%. Use dehumidifiers if needed. Avoid harsh cleaners that can damage grout or sealants. These steps help you keep your subfloor dry and strong for years.
Choosing the Best Subfloor
You can pick from many strong water resistant subfloor choices for your home. Magnesium oxide and cement board are best for wet places. They stop water, mold, and fire from causing problems. Premium OSB and engineered wood are good for most rooms and save money. Before picking, think about how much water your home might get, your budget, and what kind of floor you want.
Quick Guide:
Material | Best For |
---|---|
Magnesium Oxide | Wet, high-traffic, safe areas |
Cement Board | Bathrooms, kitchens, tile floors |
Living spaces, easy install | |
Engineered Wood | Bedrooms, moderate moisture |
If you need more help, check the MFMA website. You can find guides, videos, and expert tips about picking and caring for subfloors.
FAQ
What is the difference between water resistant and waterproof subfloors?
Water resistant subfloors slow down water damage. Waterproof subfloors block water completely. You should use waterproof materials in bathrooms or basements. Water resistant options work well in living rooms or bedrooms.
Can you install tile over any water resistant subfloor?
You can install tile over cement board or magnesium oxide panels. These materials give strong support and block water. Avoid using standard plywood or OSB under tile. They may swell or break if they get wet.
How do you know if your subfloor needs replacing?
Look for soft spots, sagging, or mold. You may see stains or smell musty odors. If you find these signs, you should check under your floor. Replace damaged subfloor to keep your home safe.
Are eco-friendly subfloor materials as strong as regular ones?
Many eco-friendly subfloors, like magnesium oxide panels, offer great strength and water resistance. You do not have to give up quality for a greener choice. Always check product ratings and certifications.
How can you protect your subfloor during construction?
Cover your subfloor with plastic sheeting or tarps. Sweep away water right away. Do not leave the subfloor exposed to rain. Quick action keeps your subfloor dry and strong.