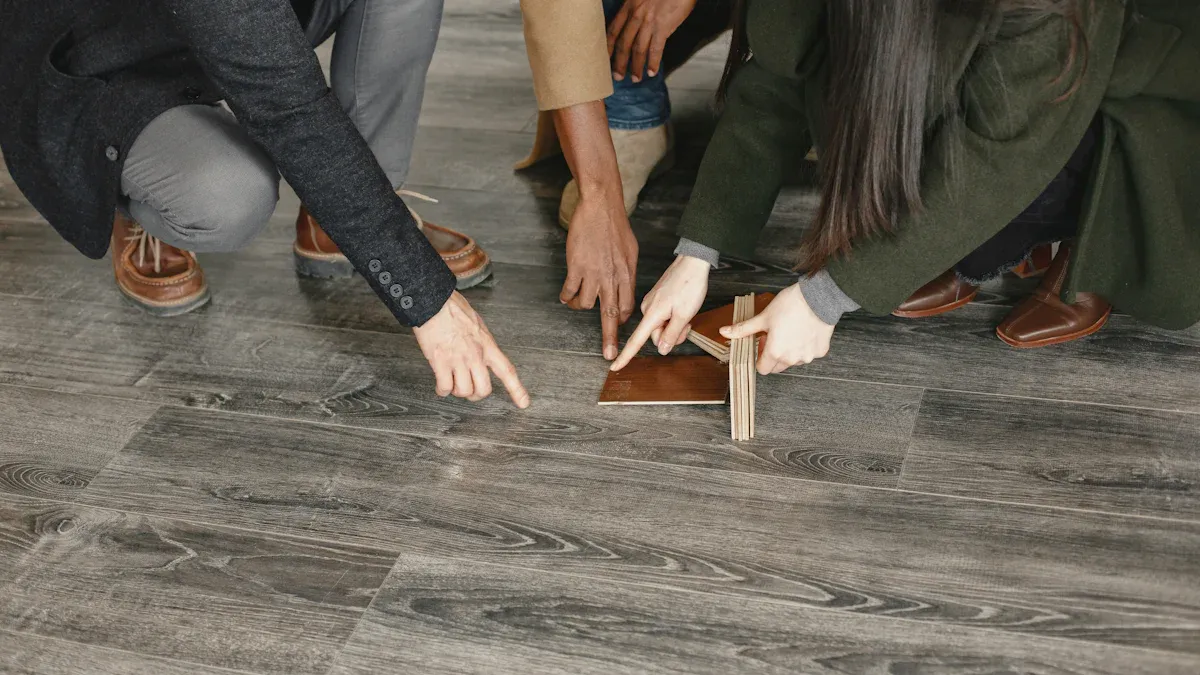
26 Jul MgO Subfloor or Underlayment Which Option Is Best for Modern Construction
Table of Contents
If you’re deciding between mgo subfloor vs underlayment for new construction, both options are excellent choices. They offer strong resistance to fire and water, making them popular among many builders today. These materials won’t bend, swell, or break down when exposed to moisture. Additionally, they contribute to cleaner indoor air quality and provide durable flooring solutions. Choosing the best option between mgo subfloor vs underlayment depends on your specific needs, including cost, installation methods, and environmental impact. Check out the summary table below for a quick comparison.
Key Takeaways
MgO panels stop water, mold, and fire. This makes floors safer and stronger in wet or risky places. – MgO subfloor or underlayment is quick and easy to put in. You use dry methods and normal tools. – MgO boards last a long time and do not break often. They cost more at first but save money later. – These panels keep the air inside clean. They stop mold and do not let out bad chemicals. – MgO subfloor and underlayment are good for homes and businesses. They make floors strong, quiet, and good for the environment.
mgo subfloor vs underlayment
Summary Table
You can use this table to see how mgo subfloor and underlayment compare. The table shows the main ways they are different. It covers things like how much they cost and how you put them in. You can also see how mgo panels and gypsum underlayment work in real buildings.
Feature | MgO Subfloor/Underlayment | Gypsum Underlayment |
---|---|---|
Installation Method | Dry install with standard tools | Wet pour, needs primers and sealing |
Curing Time | None | |
Crew Requirements | Framing crew can install | Specialty trades needed |
Moisture Sensitivity | Water- and mold-resistant | Prone to swelling, cracking, mold |
Structural Capability | Structural, direct to joists | Non-structural, needs solid base |
Scheduling Impact | Flexible, no bottlenecks | Delays, advance booking required |
Weather Impact | Installs in all conditions | Delays in humidity or bad weather |
Long-Term Maintenance | Low risk of callbacks or failures | Prone to cracking, chipping, adhesive loss |
Excellent, up to 1200°C | Moderate | |
Environmental Impact | Recyclable, low carbon footprint | Higher carbon footprint |
Upfront Cost | Higher | Lower |
Lifespan | Long, minimal maintenance | Shorter, more repairs needed |
Weight | Lightweight | Heavier |
Application | Subfloor or underlayment | Underlayment only |
Tip: If you want a strong floor that is quick to install and safer, mgo panels are better than gypsum underlayment.
Key Differences
When you compare mgo subfloor and underlayment, you notice some big differences. These differences can change how your building project goes.
Installation Process:
Mgo panels go in dry. You use normal tools. You do not have to wait for them to cure. This helps you finish faster. Gypsum underlayment needs to be poured wet. It also needs sealing and time to dry. This can slow down your project and needs special workers.Moisture and Mold Resistance:
Mgo subfloor and underlayment do not get damaged by water or mold. You can use them in places like bathrooms and basements. Gypsum underlayment soaks up water. This can make it swell, crack, or grow mold. That means more repairs and higher costs.Structural Strength:
Mgo panels are strong enough to go right on joists. This makes your floor stronger. Gypsum underlayment is not strong by itself. You must put it on a solid base and sometimes add more layers.Fire Safety:
Mgo subfloor and underlayment can handle very high heat. They protect better from fire. This is good for places where fire is a risk. Gypsum underlayment does not protect as well.Environmental Impact:
Mgo panels can be recycled and break down naturally. They are better for the planet. Gypsum underlayment is not as green and has a bigger carbon footprint.Cost and Value:
Mgo subfloor or underlayment costs more at first. But you save money later because they last longer and need fewer repairs. Gypsum underlayment is cheaper to buy, but you may pay more for fixes.Weight and Handling:
Mgo panels are light. You can carry and install them easily, even upstairs. Gypsum underlayment is heavy and harder to move.Application Flexibility:
You can use mgo panels as both subfloor and underlayment. This makes your floor system simpler. Gypsum underlayment can only be used as underlayment, so you need more layers.Enhanced Performance:
Mgo subfloor and underlayment work better in wet places, areas with fire risk, and busy spots. They also help keep rooms warm or cool by blocking heat or cold.Long-Term Results:
If you want a floor that lasts a long time, mgo panels are a good pick. They help cut down on waste and support green building.
When you pick between mgo subfloor and underlayment, think about what your project needs. If you want something strong, safe, and long-lasting, mgo panels are best. If you just need something cheap and quick, and water is not a problem, gypsum underlayment might be okay.
Durability
Structural Strength
When you pick a subfloor or underlayment, you want it to last. MgO panels are known for being very strong. DragonBoard USA tested their MgO subfloor panels with ASTM E455 rules. These tests check if the panels can hold heavy weight and not bend. Engineers look at these results to make sure your floor is safe from wind and earthquakes. MgO panels help keep your floor steady and safe.
EXACOR MgO panels have a glass fiber mesh that makes them stronger.
ICC-ES and Underwriters Laboratories check each panel for quality.
ICC Evaluation Service Report ESR-4635 shows these panels work as subfloor and underlayment.
MgO panels do not change shape or come apart, even if they get wet.
This strong performance means your floor will last a long time. You do not have to worry about your floor breaking or failing.
Impact Resistance
Floors need to handle lots of use every day. MgO panels do a great job in busy places. They do not crack, bend, or swell, even with many people walking on them. Tests show MgO boards stay strong after bending, freezing, and impact tests. They keep their shape and size over time.
MgO panels do not get damaged by dropped things or heavy furniture.
They do not swell when wet, so the floor stays smooth.
Their high alkalinity stops mold and mildew, which helps them last longer.
You can use MgO panels in busy or wet places. They are tough in hard conditions, so they are good for homes and businesses. You get a floor that works well and lasts for years.
Tip: If you want a floor that stays flat and strong, even in hard places, MgO panels are a great choice for long-lasting floors.
Moisture & Mold
Wet Area Performance
You want your floors to stay strong and safe, even in places with lots of moisture. MgO subfloor and underlayment panels give you excellent performance in wet areas. These panels do not let water in, so you do not have to worry about moisture absorption causing damage. Many builders choose MgO panels for bathrooms, kitchens, and basements because they work well in high-moisture environments.
Industry reports show that MgO panels, like EXACOR, are highly water-resistant underlayment options. They keep their shape and strength, even when exposed to moisture. You can install them faster than gypsum underlayment, which often needs time to dry and can suffer from moisture absorption. MgO panels do not swell or break down, so you get a floor that lasts longer. You also avoid the mess and delays that come with wet-laid gypsum products.
A real-world project using EXACOR MgO panels proved that these panels meet strict fire and sound standards. The panels stayed stable and did not lose performance, even when exposed to moisture. You can trust MgO panels to handle wet areas without the problems that come from moisture absorption.
Tip: If you need a water-resistant underlayment for wet spaces, MgO panels help you avoid costly repairs and keep your floors looking new.
Mold Prevention
Mold can grow fast when floors soak up moisture. You want a floor that stops moisture absorption and keeps mold away. MgO subfloor and underlayment panels resist moisture, so mold and mildew do not have a chance to grow. This makes your home or building safer and healthier.
MgO panels do not just block water. They also stop moisture from getting trapped inside the floor. This means you do not have to worry about hidden moisture absorption leading to mold problems later. Gypsum underlayment often absorbs moisture, which can cause mold to spread. With MgO panels, you get a water-resistant underlayment that protects your indoor air quality.
You can use MgO panels in places where moisture is a big problem. These panels keep your floors dry and clean. You spend less time and money fixing mold issues. Your building stays safe for everyone.
Remember: Choosing a floor with strong moisture resistance helps you prevent mold and keeps your space healthy.
Fire & Sound
Fire Resistance
You want your building to stay safe during a fire. MgO subfloor and underlayment panels give you strong fire resistance. These panels can handle very high temperatures, sometimes up to 1200°C. This means your floor will not burn or break down quickly if a fire starts. You get more time to leave the building safely.
Many building codes now require better fire resistance. MgO panels help you meet these rules. You can use them in homes, apartments, and offices. They work well in places where fire safety matters most, like kitchens, hallways, and exits. Gypsum underlayment does not offer the same level of fire resistance. It may crack or lose strength when exposed to heat.
MgO panels also help slow down the spread of fire. This gives firefighters more time to control the flames. You protect your property and the people inside. Many builders choose MgO panels because they trust their fire resistance. You can feel confident that your floor will help keep everyone safe.
Tip: For projects where fire resistance is a top concern, MgO subfloor and underlayment panels are a smart choice.
Sound Control
Noise can be a big problem in busy buildings. You want floors that block sound and keep rooms quiet. MgO underlayment panels do a great job with sound control. They help stop noise from moving between floors. This is important in apartments, hotels, and offices.
EXACOR MgO underlayment panels provide strong sound-dampening. They help you meet sound transmission (STC) and impact insulation (IIC) ratings. In many cases, you do not need to add a sound mat. This makes installation easier and saves money. Gypsum-based floors often need a sound mat to reach the same level of noise control.
A builder who used EXACOR panels said the sound deadening was a key reason for choosing MgO. The panels met both fire resistance and sound control needs. This made the project simpler and improved comfort for everyone in the building.
You can use MgO panels in multi-family or commercial spaces. They help create quiet, peaceful rooms. You get better fire resistance and sound control in one product.
Remember: MgO underlayment panels help you build safer, quieter spaces without extra steps.
Installation
Process Steps
Installing mgo subfloor or underlayment is a straightforward process. You can follow these steps to get a strong and long-lasting floor:
Prepare the surface: Remove old flooring, dirt, and debris. Sweep or vacuum the area. Make sure the surface is level and dry.
Gather materials and tools: Use mgo boards, screws, expansion bolts, and a moisture barrier if needed. Have cleaning tools and a leveling compound ready.
Cut and measure boards: Measure the space. Mark and cut mgo panels with a scoring knife or saw. Double-check your measurements.
Position and fasten boards: Lay the boards on joists. Keep edges straight and leave 3-5 mm gaps for expansion. Stagger the joints for strength. Secure the boards with screws spaced 6 inches apart on the edges and 12 inches in the middle.
Seal edges and joints: Apply sealant along seams and edges, especially in wet areas. Let the sealant dry fully.
Level the subfloor: Check for uneven spots. Sand high areas and fill low spots with leveling compound. Clean the surface again.
Install the top flooring layer: Choose a compatible floor like hardwood, vinyl, or tile. Follow the manufacturer’s instructions for installation.
Safety measures: Wear gloves, goggles, and a dust mask. Store mgo panels flat and dry.
Tip: Always leave expansion gaps between boards to prevent buckling.
Time & Labor
You can save time and effort by using mgo panels for your subfloor or underlayment. These panels often replace both layers in one step. This means you need fewer materials and less coordination between trades. You do not have to wait for a self-leveling underlayment to dry. The process is faster and cleaner. Mgo underlayment is lightweight, so you can move and install it easily. Many builders find that mgo panels help them finish projects quicker and with less labor.
mgo Installation Tips
Store mgo panels in a dry place before installation.
Use sharp tools for clean cuts.
Always check for level before laying the next board.
In wet areas, use a moisture barrier and seal all joints.
Wear protective gear to avoid dust and injury.
Follow the spacing guide for screws to keep the floor strong.
Note: If you want a smooth and durable floor, take your time with each step. Careful installation helps your mgo underlayment last longer and perform better.
Cost & Value
Upfront Costs
When you plan a new flooring project, you want to know how much you will spend at the start. MgO underlayment usually costs more than gypsum underlayment. You pay a higher price for each MgO panel. Gypsum underlayment is cheaper to buy, and many builders choose it for projects with tight budgets.
You also need to think about installation. You can install MgO underlayment with basic tools and a small crew. This saves you money on labor. Gypsum underlayment needs special workers and extra steps, like mixing and pouring. You may also have to wait for it to dry. This can slow down your project and add to your costs.
Here is a quick look at the main cost differences:
Cost Factor | MgO Underlayment | Gypsum Underlayment |
---|---|---|
Material Price | Higher | Lower |
Labor | Lower | Higher |
Installation Speed | Faster | Slower |
Equipment Needed | Basic tools | Special equipment |
Note: If you want to finish your flooring quickly and avoid delays, MgO underlayment can help you save on labor and time.
Long-Term Value
You want your flooring to last for many years. MgO underlayment gives you strong durability. Many brands, like MagPanel, offer a lifetime warranty. This means you can trust your floor to stay strong as long as you use it the right way. MgO boards resist water, mold, fire, and insects. You do not need to worry about repairs or damage from moisture.
MgO underlayment needs little maintenance.
You should store panels in a cool, dry place before you install them.
Always finish the surface to keep the boards in good shape.
Proper installation helps you get the most out of your underlayment.
Gypsum underlayment does not last as long. It can crack, swell, or grow mold if it gets wet. You may need to fix or replace it sooner. This adds to your costs over time. MgO underlayment works well in many types of flooring, from homes to busy offices. You get peace of mind knowing your floor will stay safe and strong.
Tip: If you want a floor that stands the test of time, choose MgO underlayment for its proven durability and long-term value.
Environmental & Health
magnesium oxide board Benefits
You want building materials that are good for people and the earth. Magnesium oxide board is a smart, green choice for new buildings. It gives you many environmental benefits:
Magnesium oxide board is made from natural minerals. Factories use very few chemicals, so you avoid bad substances.
Making magnesium oxide board uses less energy than other materials. This means it has a smaller carbon footprint.
You can recycle magnesium oxide board after you use it. Old boards can be used to make new ones, which cuts down on waste.
Magnesium oxide board does not give off toxins or dangerous chemicals when thrown away.
It makes less greenhouse gas than gypsum or cement during production.
Some brands, like MagPanel, even use recycled stuff in their boards.
By picking magnesium oxide board, you help the planet. You support recycling and make your building better for the earth.
Indoor Air Quality
You want your rooms to be safe and healthy. Magnesium oxide board helps you reach this goal. It does not soak up water, so mold and mildew cannot grow. This keeps your floors clean and your air fresh.
Magnesium oxide board stays flat and strong in wet places like kitchens and bathrooms.
You do not have to worry about water causing mold or germs under your floors.
Magnesium oxide board does not let out toxins or bad chemicals. This makes your home or building safer for everyone.
Its fire resistance also helps keep your space safe from fire.
Builders like magnesium oxide board because it stops moisture and germs.
When you use magnesium oxide board, you keep your air clean. You also lower the chance of health problems from mold or bad air.
Tip: If you want a healthy and green building, magnesium oxide board is a great choice for safety and peace of mind.
Project Fit
Residential vs Commercial
Think about your project before picking mgo subfloor or underlayment. In homes, mgo boards work really well in wet places like bathrooms. For example, Jeff Kudrick did a study in New Jersey using Cem-Rock Extreme mgo boards. These boards stay strong all year, even when the weather changes. They do not swell or crack, even if there is a lot of water. The big panels mean you have fewer seams. You can put in fixtures without needing extra support. This makes putting them in faster and easier than plywood or fiber-cement boards.
In buildings like offices or schools, you need tough materials that follow fire rules. Mgo boards are very good at stopping fires and last a long time. This makes them great for offices, hotels, and schools. They are strong and do not get ruined by water, so you can use them in busy kitchens or locker rooms. Most stories talk about homes, but builders also use mgo boards in big buildings because they last and help stop fires.
Tip: Mgo boards give both homes and businesses a strong, safe, and long-lasting floor.
Best Use Cases
You should pick the right product for your job. Mgo subfloor and underlayment work in many types of building projects. Here are some of the best ways to use them:
Wet places: Bathrooms, kitchens, laundry rooms, and basements do well with mgo panels because they stop water and mold.
Busy areas: Schools, hospitals, and offices need floors that can take lots of people walking. Mgo boards stay strong and keep their shape.
Fire-safe spots: Use mgo in stairs, hallways, and big buildings where fire safety matters most.
Fixing old floors: Mgo underlayment helps make old floors flat and strong without adding much weight.
Many floor layers: You can use mgo as both subfloor and underlayment, which makes your floor easier to build.
Green building: Mgo boards are good for the planet because you can recycle them and they do not make much pollution.
Fast jobs: If you need to finish quickly, mgo panels go in fast and do not need to dry.
When you use mgo, you should think about some risks:
Floor plan: Check how far apart your joists are and how big they are to pick the right mgo board.
Weight: Think about how much weight your floor will need to hold.
Frame type: Wood or steel frames change how you put in and screw down mgo boards.
Getting used to the space: Keep mgo panels in the room for 3-5 days before you put them in.
Gaps: Leave small spaces between boards and use flexible caulk to stop cracks.
Screws: Use screws that do not rust so your floor lasts longer.
Joints: Pick the right filler for seams so the joints do not break.
Note: If you plan and install carefully, mgo subfloor and underlayment will work great in any building project.
MgO subfloor or underlayment is a top pick for new buildings. Many builders like MgO because it does not let water, mold, or fire cause damage. It also goes in fast and easy. You get floors that are strong and last a long time. These floors do not need many repairs.
MgO boards give you:
Great protection from water and mold
Very good fire safety
Quick and tidy setup
Less work to keep up over the years
Think about what your project needs before you choose. Ask a building pro for advice. Look at guides or compare products to help you get the best floor.
FAQ
What is the main difference between MgO subfloor and underlayment?
MgO subfloor supports your floor structure. You install it directly on joists. MgO underlayment sits on top of a subfloor. It smooths the surface for your final flooring. Both resist water and fire.
Can you install MgO panels in wet areas like bathrooms?
Yes, you can use MgO panels in wet places. These panels do not swell or break down when wet. You get a strong, safe floor in bathrooms, kitchens, or basements.
Do MgO boards help with sound control?
MgO boards block noise between floors. You notice less sound from footsteps or voices. Many builders use MgO underlayment in apartments and offices for quieter rooms.
How long does it take to install MgO subfloor or underlayment?
You install MgO panels quickly. There is no waiting for them to dry. Most projects finish faster than with gypsum underlayment. You save time and avoid delays.
Are MgO panels safe for indoor air quality?
MgO panels do not release harmful chemicals. You get cleaner air in your home or office. These panels also stop mold and mildew, which helps keep your space healthy.