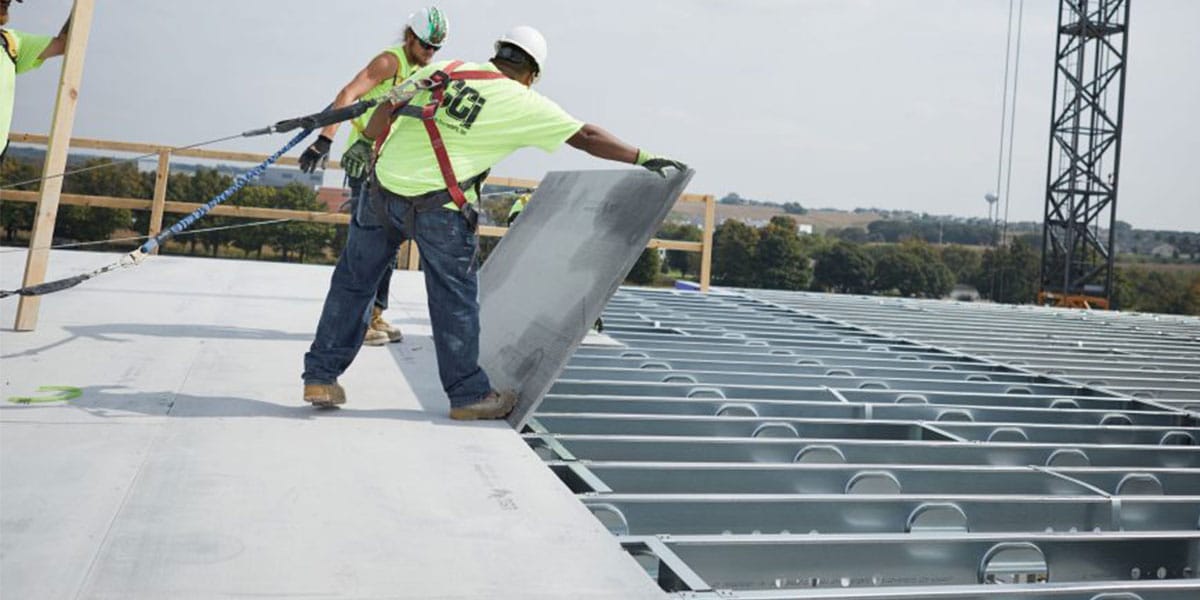
26 Jul Choosing the Right Moisture Barrier for Subfloors in 2025
Table of Contents
You need the best mgo subfloor moisture barrier in 2025. Moisture is the main reason floors fail. MgO boards and mgo panels stop moisture very well. Picking the right one is important. Each year, about 85% of floor problems are from moisture. This costs the flooring industry over $1 billion. MgO boards and mgo panels work better than other subfloor materials. They are strong and keep out water.
Demand for moisture-resistant subfloor materials has gone up:
Aspect | Details |
---|---|
Market Size (2023) | |
CAGR (2024-2030) | 10.1% growth rate |
Key Drivers | Need for durable, moisture-resistant adhesives |
You protect your floors and your money by using the right moisture barrier for mgo panels and mgo boards.
Key Takeaways
Moisture is the main reason for floor problems, so picking a strong moisture barrier keeps your floors safe and saves money. MgO boards have the best moisture resistance. They last longer and stop mold better than plywood or gypsum. Use the right moisture barrier for your subfloor type. For example, polyethylene sheets are good with OSB panels and concrete. Install the barrier the right way, like taping seams and keeping surfaces dry. This makes sure your moisture barrier works well and lasts longer. Follow 2025 building rules and use eco-friendly materials. This helps protect your floors and the environment.
Moisture Resistance in Subfloors
Why Moisture Matters
It is important to know why moisture resistance matters for subfloors. Moisture can come from many places in a building. Some common sources are:
Vapor emissions from concrete slabs can rise even if the top looks dry.
Water from leaks, rain, or broken pipes can get inside.
High humidity or water on shoes can bring in moisture.
Capillary action lets water move up from the ground through tiny spaces.
Hydrostatic pressure pushes water up when the water table is high.
If you do not have good moisture resistance, big problems can happen. Moisture can make mold grow, which is bad for your health. Wood floors might bend or change shape. Adhesives can stop working, so tiles or planks get loose. Laminate seams can get bigger and come apart. Vinyl flooring can curl at the edges. You might see white stains or grout color changes on tile floors. Over time, moisture makes the subfloor weak and repairs can cost a lot.
Tip: Always pick a subfloor system with strong moisture resistance. This will protect your money and keep your floors looking nice.
Building Trends 2025
In 2025, there are new ways to build subfloors. Builders care more about moisture resistance and water resistance now. They also want to use materials that are good for the planet. Many projects use plywood and structural hardwood. These materials come from sources that can be replaced and they resist moisture well.
Climate resilience is important too. You want subfloors that can handle tough weather and changes. Products like ClimateLine panels and Platinum “R” Floor are popular. They are strong, keep out moisture, and are easy to install. Prefabrication and modular construction are becoming more common. Lightweight and strong subfloor materials help make building faster and easier.
Building codes are changing as well. In 2025, you must follow strict rules for air tightness and air barriers. These rules help control moisture and save energy. You need to use both vapor barriers and air barriers to get the best results.
Subfloor Material Comparison
MgO Boards Overview
MgO boards are great for stopping water and lasting a long time. They stay strong even after getting wet and drying many times. In tests, MgO boards keep almost all their strength after 25 wet and dry cycles. Plywood loses about 9% of its strength, and drywall loses up to 52%. MgO panels take in very little water, only 0.34%. They do not bend, get bigger, or fall apart. Mold does not grow on MgO boards. These boards also do not burn easily, do not let water in, and can last up to 100 years with little care. They can hold heavy things and help block noise, so they are a smart pick for new floors.
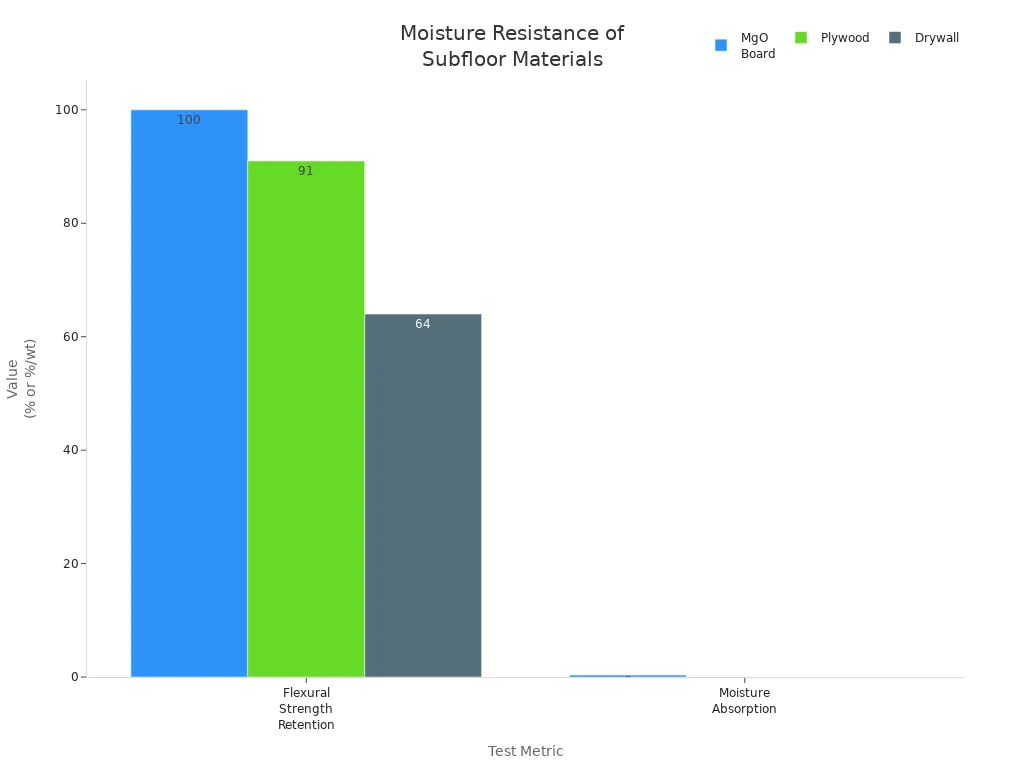
Performance Aspect | Disadvantages and Considerations | |
---|---|---|
Moisture Resistance | Excellent, no swelling or mold | |
Durability | Long-lasting, strong | Needs careful installation |
Eco-Friendliness | Recyclable, low emissions | Quality varies by brand |
Note: MgO panels are best for wet places and keep floors safe from water.
OSB and Plywood
OSB panels and plywood are used a lot for subfloors, but they do not stop water as well as MgO boards. OSB panels can get bigger and hold water longer than plywood. Both can break apart, bend, or get moldy if they get wet. After many wet and dry times, OSB panels lose strength and may not go back to their old shape. Plywood does a little better, but both can be ruined if they stay wet too long. OSB panels have wax and glue to help, but they can still swell and get mold.
OSB panels and plywood can:
Lose strength
Grow mold
Break apart
You should ask the maker before using OSB panels for subfloors in wet places.
Gypsum Underlayment
Gypsum underlayment is not good where there is water. It soaks up water fast. This makes it get bigger, crack, and grow mold. Gypsum can get soft and not hold screws or nails. In wet places, you might have to take it out and put in new flooring. You should always keep gypsum dry.
Category | Gypsum Underlayment | MAXTERRA® (Reference) |
---|---|---|
Moisture Sensitivity | High | Low |
Mold Risk | High | Low |
Durability in Humid Environments | Poor | Good |
Concrete
Concrete subfloors have a different water problem. They have tiny holes and can hold water inside. Water can move as vapor through the concrete and hurt the floor above if not stopped. You need to check concrete for water before putting down floors. Vapor barriers and sealants help stop water from moving. Concrete lasts a long time, but you must use the right ways to control water to keep floors safe.
Tip: Always check concrete for water and use a vapor barrier to keep your floors safe.
Moisture Barrier Options for Subfloors
Mgo subfloor solutions
Mgo boards are the best at stopping water. Their surface does not let water in. This means you do not worry about swelling or mold. Mgo panels stay strong in wet rooms like bathrooms. You can add a mgo subfloor moisture barrier for more safety. Most times, mgo boards work fine by themselves.
If you want extra protection, use a liquid-applied moisture barrier or a sheet membrane on top. These barriers give another layer of safety. They help if you expect lots of water or want to use special floors. Mgo subfloor moisture barrier products are simple to put in. You do not need special tools. They last a long time and help you feel safe.
Note: Mgo boards give the most moisture resistance and last a long time. They keep your floors safe from water and mold.
OSB/Plywood Solutions
Osb panels and plywood are used a lot for subfloors. They do not stop water as well as mgo boards. Osb panels can get bigger and weaker when wet. You need the right moisture barrier to keep floors safe.
Here are some good choices for osb panels and plywood:
Pick moisture-resistant subfloor products like AdvanTech plywood for damp places.
Use marine-grade plywood if you think it will stay wet.
Put vapor barriers under decks to block ground moisture.
Always fix leaks and make air flow better before adding a barrier. Do not let water get trapped under the floor.
Condition of Subfloor / Environment | Recommended Moisture Barrier Product(s) | Notes / Purpose |
---|---|---|
Concrete slab (including upper levels) | 6 mil polyethylene sheeting, taped at seams | Cheap way to control vapor |
Crawlspace or unfinished basement with occasional humidity | Red rosin paper or housewrap | Lowers vapor movement, works with osb panels |
Wooden subfloor with endemic moisture or condensation | No barrier until fixing water problems and adding ground vapor barrier | Stops trapped water that can cause damage |
Osb panels do not last as long as mgo boards in wet places. Even with sealers, osb panels can still take in water and get bigger. Always check the subfloor for water before putting down any barrier. If you use the right products and follow the maker’s tips, osb panels work better. But they still do not last as long as mgo boards in wet areas.
Gypsum Solutions
Gypsum subfloors are very weak against water. They soak up water fast and can swell, crack, or grow mold. You must test for water before putting anything on gypsum. The water in gypsum can also slow down your work.
New rules say to use better moisture barriers with gypsum. You can use polyethylene sheeting, bitumen-coated kraft paper, or rubberized asphalt membranes. These products block water and keep the subfloor dry. Aluminum foil vapor barriers and cork underlayment also help. They stop water and lower noise.
Many builders now pick MAXTERRA mgo boards instead of gypsum. MAXTERRA systems do not soak up water or grow mold. They do not need time to dry. You can use them over osb panels or as the only subfloor. This gives better water protection and lasts longer. You also meet fire and sound rules more easily.
Tip: If you use gypsum, always control the room and use a strong moisture barrier. For the best results, switch to mgo boards for long-lasting safety.
Concrete Solutions
Concrete subfloors need special care because they can hold water inside. Water vapor can move through concrete and hurt your floors. You must test how much vapor comes out before picking a moisture barrier. If the vapor is high, you need a strong barrier.
Moisture Barrier Option | Key Features and Benefits |
---|---|
Vapor Barriers under Concrete Panels | Lowers water vapor from below, keeps floors dry, and helps floors last longer. |
Concrete Subfloor Panels | Strong, water-resistant, fireproof; good for wet rooms like basements and kitchens. |
MGO Boards | High moisture resistance, do not swell or bend, mold-resistant, eco-friendly, and add insulation. |
Engineered Subfloor Panels (AdvanTech, Edge Diamond, Legacy) | Special resin for water resistance, lasts a long time, and protects edges. |
Porcelain Tiles on Concrete | Take in little water, protect the subfloor, and resist scratches and stains. |
You should always test concrete for water using ASTM F1869 or F2170. If the vapor is above 3 lbs/1000 sq. ft./day, you must use a moisture barrier. After you put down the barrier, the floor will not let water in. You may need to change glue or primer so the floor sticks well.
Callout: Always get the concrete clean, dry, and smooth before adding a moisture barrier. This helps the barrier work better and last longer.
Choosing the Right Barrier
Installation
You must put in moisture barriers the right way for good results. Always read and follow what the maker says for each product. For osb panels, put the sheets on top of each other and tape the seams. This stops water from getting in. Fix any holes or rips before you put down the floor. Doing this helps stop mold, wood rot, and wood floors from bending. If you use a liquid barrier, spread it out evenly and let it dry all the way. Good work makes your floor last longer and stay strong.
Cost
When picking a moisture barrier, think about both the price of the product and the work to put it in. For example, house wrap and labor together cost about $470 to $577 for 534 square feet. That is about $0.29 to $0.36 for each square foot. Radiant barriers cost between $0.20 and $1.00 for each square foot. Spray foam insulation costs more money, but it can make your floor last longer. Osb panels do not cost a lot, but you still need to save money for the right barrier.
Moisture Barrier Product | Installation Cost Range | Unit Basis |
---|---|---|
House Wrap | $0.29 – $0.36 | per sq ft |
Radiant Barrier | $0.20 – $1.00 | per sq ft |
Spray Foam Insulation | $3,385 – $10,960 | total project |
Durability
How long your floor lasts depends on the barrier you use. Osb panels can last many years if you use a good moisture barrier. Polyethylene sheeting and rubberized asphalt membranes are strong and help your floor stay tough. Bitumen-coated kraft paper works well under hardwood and lasts a long time. Always look for damage in the barrier before putting in the floor. A good barrier keeps working year after year and helps your floor stay strong.
Environmental Impact
Some moisture barriers are made from recycled or plant-based stuff. Many companies use water-based coatings to lower bad air chemicals. Some new barriers can break down in nature or be composted. Hybrid systems use new plastics and thin layers to work well and help the planet. Picking an eco-friendly barrier helps you build green and make less trash.
Tip: Pick products with recycled parts or LEED labels if you want a greener house.
Flooring Compatibility
You need to match the barrier to your floor type. Polyethylene sheeting is good for concrete and osb panels. Bitumen-coated kraft paper is best for hardwood floors. Rubberized asphalt membranes and cork underlayments help with sound and water for laminate and vinyl. Some barriers, like epoxy coatings, protect many kinds of floors in homes, offices, and warehouses. Always check what the floor maker says to get the right barrier.
2025 Product Recommendations
Top Sheet and Liquid Barriers
You want the best protection for your subfloors. In 2025, top-rated sheet and liquid barriers help keep floors dry and safe. Many new products use advanced technology to stop water from getting through. You can find these barriers in both sheet and liquid forms. Some of the most trusted options include:
Coretec uses a limestone core that repels water. Its edge treatments and surface coating make it fully waterproof.
Shaw’s Floorté Pro Series has a multi-layer system. It works well in places with lots of moisture, like basements and bathrooms.
Mohawk’s SolidTech uses Hydroseal technology. Its watertight barrier and special joints keep out spills for up to 24 hours.
Armstrong’s Luxe Plank with WaterGuard Defense Solutions has a polymer coating and edge-sealing. Its locking system stops water from getting in.
These products often come as part of luxury vinyl tile flooring. They work well over osb panels, mgo boards, and even concrete. If you use a liquid-applied barrier, you can paint or roll it on top of your subfloor. This method works for both osb panels and mgo panels. Sheet membranes are easy to lay down and tape at the seams. You get a strong layer that blocks water and helps your floor last longer.
Tip: Always check if your chosen barrier matches your subfloor type and flooring material.
Best for MgO Boards
You want the right mgo subfloor moisture barrier for your project. MgO boards already resist water better than osb panels or gypsum. Most of the time, you do not need extra protection. If you want more safety, pick a liquid-applied barrier or a thin sheet membrane. These options add another layer without making the floor too thick.
Here is a quick guide for choosing a barrier for mgo boards:
Subfloor Type | Best Barrier Type | Why It Works |
---|---|---|
MgO boards | Liquid-applied membrane | Seals seams, adds water resistance |
MgO panels | Sheet membrane | Easy to install, blocks moisture |
OSB panels | Polyethylene sheeting | Stops vapor, protects wood fibers |
You can use these barriers with many floor types, including vinyl, laminate, and tile. Always follow the maker’s instructions for the best results. When you use mgo boards with a proper mgo subfloor moisture barrier, you get a floor that stands up to water, mold, and daily wear. Osb panels need more care and stronger barriers to last as long as mgo boards.
Installation Tips
Preparation
You need to start with a clean and dry subfloor. Sweep away dust and debris. Check for any signs of moisture damage, swelling, or mold. If you see problems, fix them before you move on. Look at the type of subfloor you have. If you use osb panels, make sure they are flat and not swollen from water. Pick the right moisture barrier for your subfloor. For example, use a plastic sheet for concrete or foam for wood. Always follow the manufacturer’s instructions and local building codes.
Tip: A smooth and dry surface helps your moisture barrier work better and last longer.
Application
Begin in one corner of the room. Lay out the moisture barrier sheets over your osb panels. Overlap each sheet by at least 6 inches. This overlap stops water from getting through the seams. Tape all seams carefully. Make sure you seal around pipes and ducts. If you use a liquid barrier, spread it evenly with a roller or brush. Let it dry fully before you install flooring. For osb panels, keep the barrier flat and free of wrinkles or bumps. This step prevents uneven floors later.
Steps for installing a moisture barrier over osb panels:
Clean and inspect the osb panels.
Lay the barrier, overlapping sheets by 6 inches.
Tape all seams and seal edges.
Smooth out any wrinkles.
Let the barrier settle before adding flooring.
Common Mistakes
Many people rush the job and miss important steps. You might forget to tape seams or leave gaps around pipes. Wrinkles or bumps under the barrier can cause problems with your flooring. Some skip checking the osb panels for moisture or damage. Using the wrong barrier for your subfloor type can lead to failure. If you do not follow the instructions, you risk mold, swelling, or loose floors.
Callout: Take your time and check your work. Careful installation protects your osb panels and keeps your floors safe for years.
You now know the best moisture barrier for each subfloor. MgO boards give you top moisture resistance and long-lasting protection. For OSB or plywood, use a strong sheet or liquid barrier. Gypsum needs extra care with a high-quality membrane. Concrete works best with a tested vapor barrier. Always follow 2025 building standards. When you choose the right system, you protect your floors for years. For more help, check local codes or talk to a flooring expert.
FAQ
What is the main reason to use a moisture barrier under subfloors?
You use a moisture barrier to stop water from damaging your floors. It keeps out mold, swelling, and rot. This helps your floors last longer and look better.
Can you install a moisture barrier by yourself?
Yes, you can install most moisture barriers yourself. Follow the product instructions. Use tape for seams and smooth out wrinkles. If you feel unsure, ask a flooring expert for help.
Do MgO boards always need an extra moisture barrier?
MgO boards resist water very well. In most cases, you do not need an extra barrier. For wet rooms or extra safety, you can add a liquid or sheet barrier on top.
How do you test if your subfloor has too much moisture?
You can use a moisture meter or a simple plastic sheet test. Tape plastic to the floor and check for water drops after 24 hours. If you see moisture, you need a barrier.
Which moisture barrier works best for vinyl flooring?
A polyethylene sheet or a liquid-applied membrane works best under vinyl. These barriers stop water vapor and protect both the subfloor and the vinyl. Always check the flooring manufacturer’s guide for the best match.