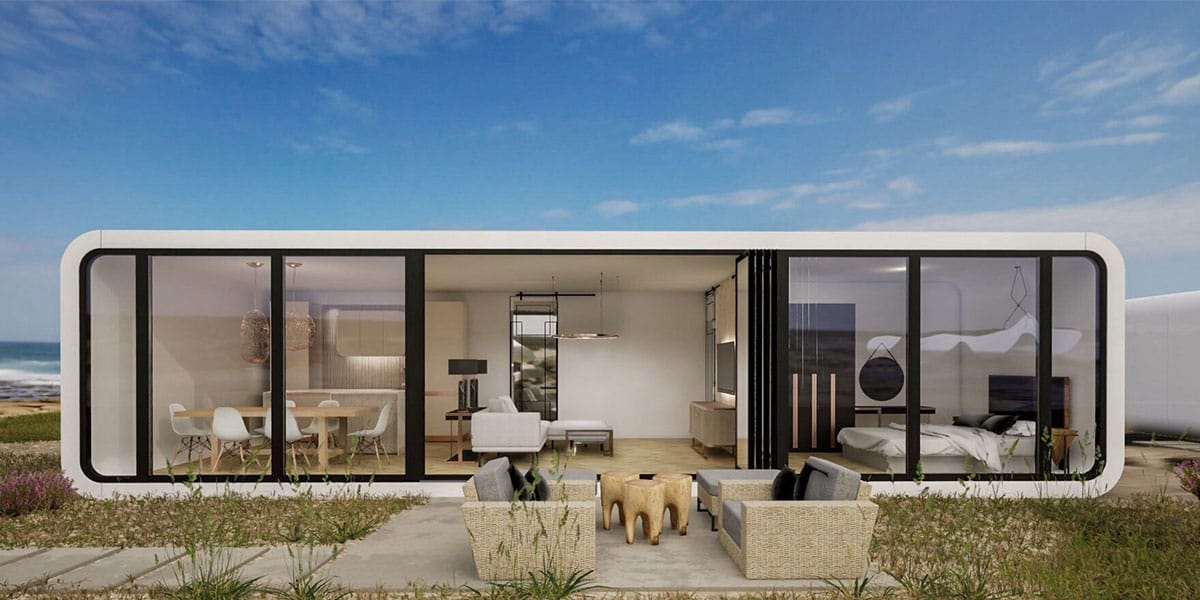
21 Jul 7 Tips for Picking the Right Subfloor Thickness for Your Mobile Home
Table of Contents
You want your mobile home to feel solid underfoot, right? For 2025, most experts recommend a mobile home subfloor thickness of 3/4 inch plywood or 23/32 inch OSB. Many people also turn to MGO panels for extra fire and moisture resistance. When you pick flooring, you need to think about how it will work with your subfloor. Some flooring options need a stronger base. Other types of flooring handle moisture better. Your home’s age, the climate you live in, and the kind of flooring you like all play a big role in your final choice.
Key Takeaways
Pick a subfloor that is 3/4 inch plywood or 23/32 inch OSB. This makes your floor strong and steady. It helps stop the floor from sagging or feeling soft.
Make sure your subfloor thickness matches your joist spacing and flooring type. This keeps your floor safe and comfy.
Use moisture-resistant materials like MGO panels or exterior-grade plywood in wet places. This helps protect your floor from mold and water damage.
Look at your subfloor for any damage before you put in new flooring. Fix weak spots early to save money and stop problems later.
Follow local building codes and what the manufacturer says. This makes sure your floor is safe, lasts long, and meets insurance rules.
Mobile Home Subfloor Thickness
2025 Standards
When you look at mobile home subfloor thickness, you want to follow the latest advice. For 2025, experts say you should use 3/4 inch plywood, 23/32 inch OSB, or MGO panels. These materials give your mobile home a strong base. You need this strength for all types of flooring. If you pick carpet, vinyl, tile, or laminate, the right mobile home subfloor thickness keeps your floors safe and steady.
Tip: Thicker subfloors help stop soft spots and sagging. You will feel more comfortable walking around your home.
Why does mobile home subfloor thickness matter so much? Here are some reasons:
Thicker subfloors last longer and handle heavy furniture better.
You get fewer problems with moisture, like warping or rot.
Your flooring will not crack or shift as easily.
You avoid safety risks, such as tripping over uneven spots.
The right thickness supports all types of flooring, even heavy tile.
If you use thin subfloors, you might see soft spots or even holes. This can make your flooring wear out faster. You may also notice squeaks or dips when you walk. Fixing these problems later costs more money and time.
Joist Spacing Impact
Joist spacing is the distance between the beams under your floor. Most mobile homes have joists 16 or 24 inches apart. The wider the space, the more important mobile home subfloor thickness becomes. If your joists are far apart, you need a thicker subfloor to keep your flooring from bending or breaking.
For 16-inch spacing, 3/4 inch plywood or 23/32 inch OSB works well.
For 24-inch spacing, you should use the thickest subfloor you can, like MGO panels or extra-strong plywood.
Always match your mobile home subfloor thickness to your joist spacing and your flooring type. This way, you get a safe, sturdy, and comfortable home.
Subfloor Material Options
When you choose a subfloor, you want it strong and safe. It should last a long time in your mobile home. The main choices are plywood, OSB, and MGO panels. Each one is good for different reasons. Each has some downsides too. You need to pick the right one for your needs. Think about what kind of flooring you want to use.
Best Plywood for Mobile Home Subfloor
Many people like plywood for their subfloor. It gives strong support for all flooring types. The best plywood for mobile home subfloor is 3/4 inch thick and exterior-grade. This plywood holds nails and screws tightly. Your flooring will stay flat and secure. Plywood dries out fast if it gets wet. This helps stop swelling and rot. You can use plywood under tile, vinyl, laminate, or carpet. Plywood lasts a long time and can add value to your home.
Here’s a quick look at how plywood and OSB compare:
Feature | Plywood Advantages | OSB Advantages and Disadvantages |
---|---|---|
Structural Strength | Stronger, more rigid, better nail/screw holding power | Slightly weaker, more flexible, but has twice the horizontal shear strength |
Moisture Resistance | More resistant to permanent swelling, dries faster | Edges swell when wet, holds moisture longer |
Suitability for Flooring | Suitable for all flooring types including heavy tiles | Not recommended under ceramic or stone tile |
Cost | About $21 per 4×8 sheet | Cheaper, about $16 per 4×8 sheet |
Installation | Easier to install, requires fewer fasteners | May need more fasteners |
Durability | Lasts as long as the house if kept dry | Lasts as long as house if kept dry, but more flexible |
Resale Value | Slightly preferred by buyers | Less preferred due to cheaper look |
Tip: Do not use particleboard or MDF for your subfloor. These soak up water very fast. They break down easily. Your flooring will not last if you use them.
OSB and MGO Panels
OSB costs less than plywood. It works well in dry places. You can use OSB under carpet, vinyl, or laminate. It does not work well with tile or in wet areas. OSB edges can swell if they get wet. This can ruin your flooring over time.
MGO panels are a newer choice. They block water and do not burn. They also stop mold from growing. If you live where it is wet or humid, MGO panels keep your flooring safe. They also help protect your home from fire. MGO panels last a long time and do not crack under heavy things. They are better for the environment than plywood or OSB. MGO panels use natural minerals. They make less pollution. They even help trap carbon dioxide when made.
Here’s a table to help you compare MGO panels and OSB:
Property | MGO Panels (Magnesium Oxide Boards) | OSB Panels (Oriented Strand Board) |
---|---|---|
Fire Resistance | Non-combustible, safer in fire situations | Can burn, not fire resistant |
Moisture Resistance | Blocks water, resists mold and rot | Edges absorb water, can swell and weaken |
Durability | Strong, resists impacts, does not crack | Strong but can weaken with moisture |
Recommended Use | Best for wet or humid climates, all flooring types | Best for dry areas, not for tile or wet areas |
If you want a subfloor that lasts and keeps your flooring safe, MGO panels are a smart pick. They also help the planet. OSB can work if you have a small budget and live in a dry place. But you must keep OSB dry.
Home Age and Structure
Older vs. Newer Homes
When you look at your mobile home, the year it was built makes a big difference in your subfloor options. Older mobile homes often have subfloors made from particle board or MDF. These materials soak up moisture like a sponge. Over time, they get soft, crumbly, and weak. You might notice your floor feels bouncy or even see soft spots. These old subfloors are not strong enough to hold up heavy furniture or new flooring.
Newer mobile homes usually have OSB subfloors. OSB stands up better to water and lasts longer. You get a sturdier floor that feels solid under your feet. If you have an older home with a weak subfloor, you can fix it by adding a new layer on top. Most people use 3/4″ tongue-and-groove OSB or plywood for this job. This overlay brings back the strength your floor needs.
Here’s what you should keep in mind:
If your old subfloor is particle board or MDF, add a 3/4″ OSB or plywood overlay.
For higher-quality pressed-particle subfloors, you can use a thinner overlay like 1/2″ or 5/8″ BC plywood.
In living areas, exterior-grade plywood works best.
For bathrooms or kitchens, cement board or hardybacker gives better moisture protection.
Try not to use overlays thicker than 1/2″ if you worry about the nailing surface for your walls.
Tip: Always check your subfloor before installing new flooring. Fixing weak spots now saves you trouble later.
Structural Support
The way your mobile home is built also affects your subfloor choice. Mobile homes do not have a solid foundation like regular houses. Instead, they use metal or wood joists spaced to handle certain weights. Older homes often have wider joist spacing and weaker materials. This can lead to uneven floors, creaks, or even sinking if you do not upgrade your subfloor.
Particle board and MDF in older homes absorb moisture and break down fast.
OSB in newer homes gives better support and resists water damage.
Weak subfloors can cause safety risks, like tripping or falling.
Always match your subfloor thickness to your home’s structure and joist spacing.
If you want a floor that feels safe and lasts for years, choose the right subfloor for your home’s age and structure. Your feet—and your furniture—will thank you!
Moisture and Climate
Wet Area Solutions
Moisture can cause big problems in your mobile home, especially in places like bathrooms, kitchens, and laundry rooms. You want your flooring to last, so you need to pick the right subfloor and finish materials. MGO panels and exterior-grade plywood work best under flooring in wet areas. These materials resist water and help stop mold and rot. If you use the wrong subfloor, your flooring can warp, swell, or even fall apart.
When you choose flooring for wet spaces, look for options that handle water well. Here are some top picks:
Vinyl plank flooring stands out as 100% waterproof flooring. It works great in humid places and keeps your floors safe from spills.
Tile flooring, like ceramic or porcelain, is tough and waterproof. It’s perfect for bathrooms and kitchens.
Epoxy flooring gives you a smooth, waterproof surface. It’s a smart choice for laundry rooms or utility spaces.
You also need to think about how you install your flooring. Make sure your subfloor is level and dry before you start. Use waterproof sealants around the edges. Good ventilation helps too. Open windows or use exhaust fans to keep air moving and cut down on moisture.
Tip: Always check for leaks under sinks and around toilets. Fixing small leaks early keeps your flooring in good shape.
Dry Climate Choices
If you live in a dry place, like Arizona or Nevada, you have an advantage. Dry air helps your flooring and subfloor last longer. Water damage is the main reason wood-based subfloors break down. In dry climates, you don’t have to worry as much about rot or mold. Plywood and OSB both work well under your flooring in these areas.
Homes in dry regions often stay in good shape for over 50 years. You still need to keep your flooring clean and check for any signs of damage. Even in dry places, spills can cause trouble if you don’t clean them up. Choose flooring that fits your style and needs, but remember that wood-based subfloors hold up better when moisture stays low.
Good airflow helps your flooring last. Open windows when you can, and don’t let water sit on your floors.
Best Flooring for Mobile Homes
Best Type of Flooring for a Mobile Home
You want your home to look great and feel comfortable. Picking the best flooring for mobile homes can make a big difference. Each room in your home has its own needs. Some rooms get wet, while others stay dry. You might want something soft under your feet or a floor that is easy to clean.
Let’s look at the best type of flooring for a mobile home:
Luxury vinyl plank stands out as one of the best flooring for mobile homes. It is waterproof, easy to install, and comes in many styles. You can use it in kitchens, bathrooms, or living rooms.
Laminate flooring gives you a wood look without the high price. It works well in living areas and bedrooms.
Carpet feels soft and warm. It is a good choice for bedrooms or places where you want comfort.
Tile is strong and waterproof. It is perfect for bathrooms and kitchens but needs a solid subfloor.
When you choose the best type of flooring for a mobile home, think about where you will use it. Wet areas need waterproof floors. High-traffic spots need something tough. The best flooring for mobile homes should match your lifestyle and budget.
Subfloor Compatibility
The right subfloor helps your new flooring last longer. Most mobile homes use plywood or OSB as subfloors. These materials are strong and light. They work well with many flooring options for mobile homes.
Here are some good subfloor materials for luxury vinyl plank:
Foam: Works with plywood, but does not block moisture.
Cork: Stops mold and gives good sound insulation.
Felt: Thin but eco-friendly and quiet.
Rubber: Great for moisture and keeps floors warm.
Plywood: Strong and resists water better than particleboard.
OSB: Durable and handles moisture well.
You should avoid particleboard. It is cheap but does not last long or handle water. For the best flooring for mobile homes, always pair your flooring with a solid subfloor. For tile, use thick plywood or MGO panels. For vinyl or laminate, plywood or OSB works best. Carpet can go over most subfloors, but you still want a smooth, dry surface.
Tip: Always check your subfloor before installing new flooring. Fixing weak spots now saves you money and trouble later.
When you match the right subfloor with your flooring, you get a home that feels safe and looks great. The best flooring for mobile homes starts with a smart choice under your feet.
Codes and Recommendations
Building Codes
You want your mobile home to be safe and up to date. Local building codes help you do that. These codes tell you what materials and thickness you can use for your subfloor. They also set rules for things like fire safety and moisture protection. If you skip these rules, you might face big problems later.
Before you start any subfloor project, check with your city or county office. Ask about the latest codes for mobile homes. Some places have special rules for mobile homes that are different from regular houses. You might need a permit before you begin. If you follow the codes, you protect your home and your family.
Note: Insurance companies often ask if your home meets local codes. If you do not follow them, you could lose coverage after a claim.
Here is a quick checklist for building code steps:
Call your local building department.
Ask about subfloor thickness and approved materials.
Find out if you need a permit.
Keep all paperwork for your records.
Manufacturer Guidelines
Manufacturers know their products best. They test subfloor materials and give you clear instructions. Always read the guidelines that come with your plywood, OSB, or MGO panels. These instructions tell you how to install the subfloor, what fasteners to use, and how to space the panels.
If you ignore these guidelines, you might void your warranty. You could also end up with a floor that squeaks or sags. Manufacturers want you to get the best results, so trust their advice.
Tip: Save the installation guide and warranty card. You might need them if you have questions later.
When you follow both local codes and manufacturer guidelines, you get a strong, safe, and long-lasting floor. You also make sure your insurance stays valid. Take the time to check the rules before you start. Your future self will thank you!
Budget and Longevity
Cost vs. Durability
When you pick new flooring for your mobile home, you might want to save money. It feels good to find a deal. But sometimes, the cheapest choice costs you more in the long run. Thin subfloors or low-quality materials can wear out fast. You may see soft spots, squeaks, or even water damage. Fixing these problems means spending more money later.
If you invest in high-quality subfloor materials, you get better moisture protection, insulation, and comfort. Your flooring will last longer and look better. You will not need to repair or replace it as often. For example, magnesium boards resist water, mold, and fire. Engineered wood panels do not warp or shrink. Concrete subfloors stay strong, even in busy or wet areas. These choices help you avoid costly repairs.
Tip: Spending a little more now on good subflooring can save you a lot of money and stress in the future.
Here’s a quick look at how different subfloor materials affect your budget:
Material | Upfront Cost | Maintenance Needs | Lifespan |
---|---|---|---|
Plywood | Medium | Low | 20+ years |
Low | Medium | 10-20 years | |
MGO Panels | High | Very Low | 30+ years |
Concrete | High | Very Low | 40+ years |
Future-Proofing
You want your mobile home to feel safe and sturdy for years. Choosing the right flooring and subfloor now helps you avoid headaches later. If you pick materials that handle water, heat, and heavy use, you will not worry about damage. MGO panels and concrete subfloors work well in kitchens and bathrooms. They keep your flooring dry and strong.
Think about your future plans. Will you want to change your flooring style? A strong subfloor lets you switch from carpet to tile or vinyl without trouble. If you use a cheap and resilient flooring option, you get both savings and durability. You can enjoy your home without worrying about repairs.
Invest in quality subflooring for less maintenance.
Pick materials that match your climate and lifestyle.
Plan for changes by choosing a strong, stable base.
Your choices today shape your comfort and costs tomorrow. Make your flooring last by thinking ahead.
Quick Reference Table
Thickness and Material by Scenario
It can be tough to remember every detail for your mobile home. This table helps you pick the best subfloor thickness and material for each situation. Use it when you plan new floors or need to fix a spot.
Tip: Check your joist spacing before picking your subfloor. The right match helps your flooring last longer.
Scenario | Recommended Thickness | Best Material | Flooring Compatibility | Notes |
---|---|---|---|---|
Wet areas (bath, kitchen, laundry) | 3/4″ (19mm) | Vinyl, tile, waterproof plank | Blocks moisture, stops mold | |
Dry climate, living spaces | 23/32″ (18mm) | Carpet, laminate, vinyl | Good for most flooring types | |
Joists 16″ apart | 3/4″ (19mm) | Plywood or OSB | Any flooring | Standard for most mobile homes |
Joists 24″ apart | 1″ (25mm) | MGO or double plywood | Tile, heavy flooring | Extra strength for wide spacing |
Overlay on old subfloor | 1/2″ (13mm) | Plywood | Any flooring | Use over weak or damaged subfloors |
High-traffic entryways | 3/4″ (19mm) | MGO or Plywood | Tile, vinyl plank | Handles heavy use and moisture |
Each situation needs its own subfloor thickness and material. Wet rooms need strong, water-resistant subfloors. Living rooms and bedrooms do well with plywood or OSB. If you want tile or stone, use a thicker subfloor for more support.
If you might change your flooring later, start with a strong base. This makes upgrades simple and keeps your home safe. Use this table when you buy materials or talk to a contractor.
Remember: Picking the right subfloor helps your flooring look good and last longer!
When you pick subfloor thickness, focus on getting a level and securely fastened base. This keeps your floors strong and looking good for years.
Make sure your subfloor is flat and tight to stop damage or squeaks.
Use quality materials and seal edges, especially if you plan to replace flooring in mobile homes or install new subflooring.
If you feel unsure, check expert guides or talk to a pro. You’ll find step-by-step help and real stories from other homeowners.
FAQ
What is the best subfloor thickness for a mobile home?
You should use 3/4 inch plywood or 23/32 inch OSB. These give your floor strength and help stop sagging. If you want extra protection, MGO panels work well too.
Can I put new subfloor over old particle board?
Yes, you can. Lay 1/2 inch or 3/4 inch plywood or OSB right on top. Make sure the old floor is dry and flat. This gives you a strong, safe base for new flooring.
How do I know if my subfloor needs replacing?
Look for soft spots, squeaks, or sagging. If you see water damage or mold, you should replace the subfloor. Tap the floor—if it feels weak or sounds hollow, it’s time for an upgrade.
What subfloor material works best in wet areas?
MGO panels and exterior-grade plywood resist water and mold. Use these in bathrooms, kitchens, and laundry rooms. They help your floors last longer and stay safe.
Do I need a permit to replace my mobile home subfloor?
Check with your local building office. Some places require a permit for subfloor work. Always follow local codes to keep your home safe and your insurance valid.