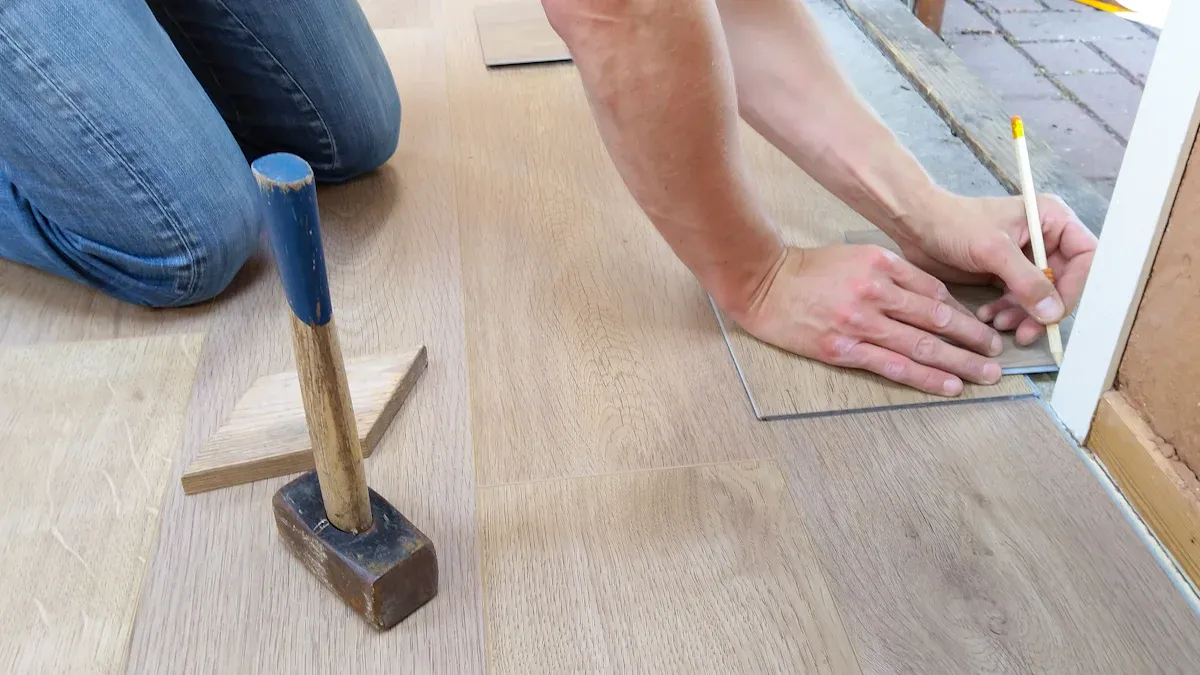
27 Jul How to Insulate a Floor on Top of a Subfloor
Table of Contents
You can insulate floor on top of subfloor using rigid foam boards or magnesium board. These materials are effective in saving energy and increasing your home’s comfort. Make sure to seal every seam and include a vapor barrier to maximize energy efficiency. Additionally, lay down an underlayment to protect the floor and improve its feel. Most DIYers can complete this project with basic tools for added energy savings.
Key Takeaways
Pick the best insulation material, like rigid foam boards or magnesium board. This helps save energy and keeps your home cozy.
Get the subfloor ready by cleaning it. Fix any damage and make sure it is flat. Do this before you add insulation for the best outcome.
Cut the insulation boards so they fit tightly. Make sure the seams are staggered to stop heat from escaping. This helps your home use less energy.
Seal every seam and gap with tape or caulk. This stops drafts, moisture, and pests from hurting your insulation.
Always put down a vapor barrier and underlayment. This keeps moisture away from your floor. It also makes your floor more comfortable and quieter.
Materials for Subfloor Insulation
When you want to insulate a subfloor, picking the right materials is important. This helps save energy and makes your home more comfortable. Many people use rigid foam boards, magnesium board, or fiberglass insulation. Each one has its own good points for different needs and budgets.
Rigid Foam Boards
Rigid foam boards are a common choice for subfloor insulation. You can pick from expanded polystyrene (EPS), extruded polystyrene (XPS), or polyiso boards. Polyiso keeps floors warmer with less thickness because it has the highest R-value per inch. EPS and XPS also keep heat in and block moisture well. Rigid foam boards do not bend easily and last a long time. They are also a good deal for most homes. If you want to save energy, rigid foam is a smart pick.
Material | R-Value per Inch | Key Characteristics |
---|---|---|
Polyiso Rigid Board | 5.6 – 8 | Highest R-value, moisture resistant, durable, eco-friendly |
EPS (Expanded Polystyrene) | 3.6 – 4 | Moisture resistant, cost-effective, good compressive strength |
XPS (Extruded Polystyrene) | 4.5 – 5 | High compressive strength, moisture resistant |
Fiberglass Insulation | 2.8 – 3.9 | Cost-effective, moderate R-value, less suitable for moist environments |
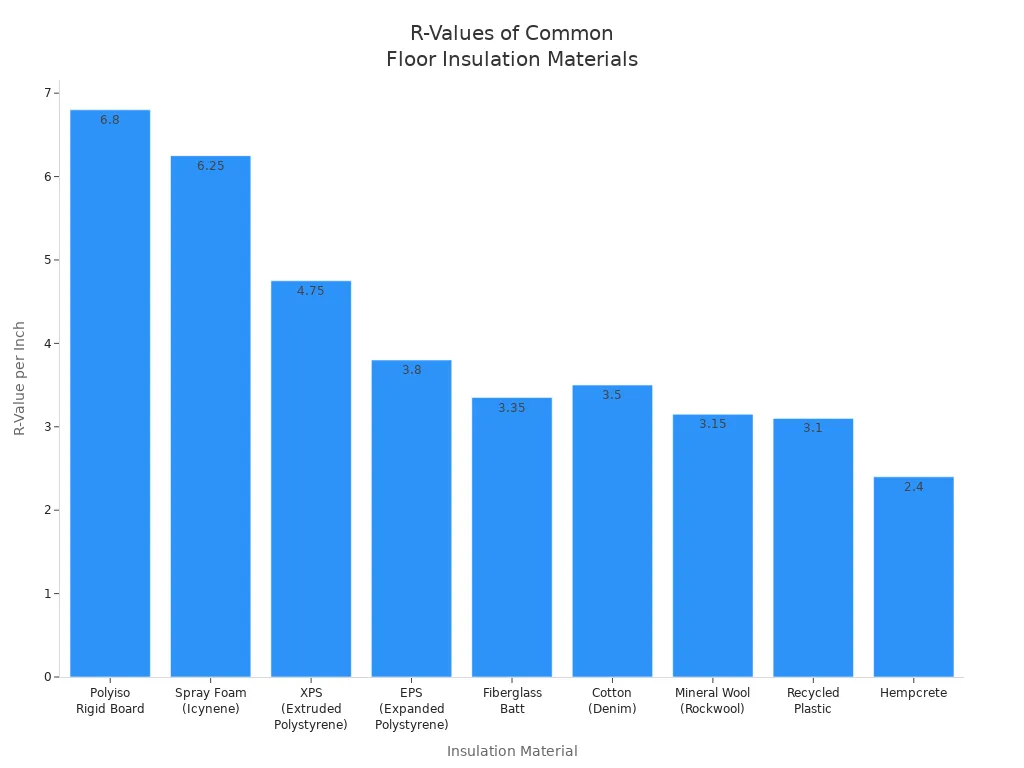
Fiberglass insulation does not work well in wet places. It is best for dry areas where water is not a problem.
Magnesium Board
Magnesium board is another good choice for subfloor insulation. It is great because it does not burn and keeps out water. You can use magnesium board in basements, bathrooms, or other damp places. This board does not catch fire, stops mold, and stays strong even if it gets wet. Magnesium board is also good for the environment and does not make toxic smoke in a fire. It gives you a safe, strong, and green way to insulate your floors.
Tools Needed
You only need basic tools for most subfloor insulation jobs. Here is a list to help you get ready:
Utility knife for thin boards or saws for thick boards
Safety goggles, gloves, and a dust mask
Pry bar and hammer
Floor scraper and broom
Construction adhesive
Screws or nails that do not rust
36-inch level to check if the floor is flat
Rubber mallet to fit boards in place
Tip: Always wear safety gear and keep your area clean for the best results.
You should also use an underlayment and a vapor barrier with your insulation. The underlayment makes the floor smoother, blocks noise, and feels better. The vapor barrier keeps water away from your floor. This helps stop warping, mold, and damage. These layers help keep your home warm, dry, and quiet.
Insulate Floor on Top of Subfloor
Preparation
You need to get the area ready before you start. Good prep helps your insulation last and work well. Here are some steps to follow:
Look at the subfloor for damage or wet spots. Fix any loose boards or holes.
Clean the floor. Use a vacuum and a damp mop to remove dirt and glue.
Make the floor flat with patching or leveling compounds.
Check for moisture. If it is damp, put in a moisture barrier.
Add an underlayment. This helps with sound, insulation, and comfort.
Check again to make sure the floor is dry, clean, and level.
Tip: If the floor is very uneven, do not try to fix it yourself. Call a pro for big repairs. For small bumps, a good underlayment can help and stop noise.
Cutting Insulation
Cutting insulation the right way is important for a good fit. Here is how you can do it:
Measure each part of the floor two times before cutting. This stops gaps that let heat out.
Mark your lines with a pencil or chalk that stays on.
Keep your work area flat and clean for easy cutting.
Use a sharp utility knife or saw. Change blades often for smooth cuts.
Use a straightedge to guide your cuts.
For thick boards, cut gently a few times instead of one deep cut.
Hold both sides of the board so the edges stay neat.
Plan your cuts to use less material and waste less.
Wear gloves, goggles, and a dust mask to stay safe.
Keep the room aired out and clean up scraps right away.
Note: Boards that fit tight work better and save energy. Gaps or loose boards make insulation less effective.
Installation Steps
Now you can put in the insulation. Follow these steps for a smooth job:
Start in a corner. Lay the first board flat on the subfloor.
Stagger the seams like bricks. This stops heat from leaking.
Push each board close to the next one. Use glue or fasteners if needed.
Fill small gaps with spray foam or caulk to block air.
If the room is damp, add a vapor barrier. Overlap and tape the edges.
Put the underlayment on top of the insulation. This adds comfort and protects the floor.
Finish with your flooring, like laminate, hardwood, or carpet.
Callout: Always check your local building codes for the right R-value. The chart below shows the minimum R-values and maximum U-factors for different areas:
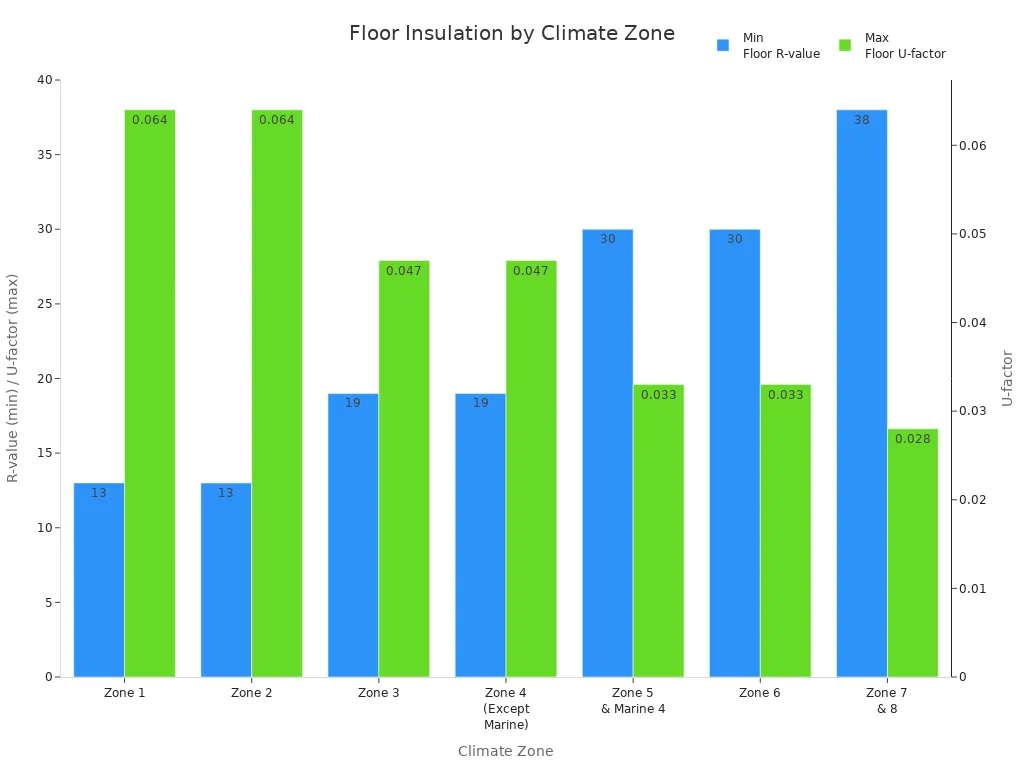
Sealing and Air Barrier
Sealing is very important when you insulate a floor. Good sealing keeps out drafts, water, and bugs. It also helps your insulation work better.
Use strong acrylic tape like JointSealR or HomeSealR for seams. These tapes stick well and last long.
For small gaps, use polyurethane caulk. This caulk stays flexible and keeps sealing.
If pipes or wires go through, use liquid flashing or flexible sealant to close holes.
Press tape down hard and make sure the surface is clean before sealing.
Tip: Seal both the insulation and the finished floor for the best protection from air leaks and water.
Room Height Loss and Solutions
Adding insulation and underlayment will make your floor a bit higher. Most floors go up by a few millimeters to about 1 inch, depending on what you use.
Pick thinner underlayment if you want less height change.
Match the new floor height to other rooms for smooth steps.
Use reducer moldings to handle height changes between rooms.
If needed, have a pro level the subfloor before you start. This keeps the floor safe and even.
Note: Planning for height changes stops tripping and keeps your home neat.
Description | How to Overcome | |
---|---|---|
Product Defects and Delivery | Problems with insulation or late delivery can slow you down. | Check insulation when it arrives; work with suppliers who replace items fast. |
Poor Timing with Other Trades | Working with other contractors at the same time can cause delays and safety problems. | Talk with contractors and plan ahead to avoid problems. |
Limited Space for Insulation | Not enough space may mean using thin insulation, which does not work as well. | Ask distributors for products that fit the space but still have a good R-value. |
Improper Sealing and Air Barriers | Air leaks can cause water, mold, and damage, especially at seams and holes. | Seal well and install air barriers the right way to stop leaks. |
Improper Use of PPE | Not using safety gear right can be dangerous. | Use the right PPE and put it on and take it off the right way. |
Environmental Challenges | Water, temperature changes, bugs, and heat can hurt insulation or cause problems. | Store materials right; pick products for your area; get ready for weather. |
Lack of Training | Bad installation often happens when people are not trained. | Give good training on insulation and how to install it. |
If you follow these steps, you can insulate your floor with confidence. Good prep, careful cutting, correct installation, and sealing help your insulation work best. This keeps your home warmer, drier, and saves energy.
Tips for Insulating Subfloor
Maximizing Efficiency
You can make subfloor insulation work better by using some smart steps. Always put the seams of your insulation boards in a staggered pattern. This stops heat from getting out and keeps your floor warm. Pick the right thickness for your insulation boards. Thicker boards have a higher R-value, so they save more energy. If you use electric underfloor heating, put thermal insulation under the heating mats. This helps push heat up and saves energy.
Here are some ways to make your home more efficient and comfortable: 1. Use programmable thermostats to set heating times and save money. 2. Split your home into zones so you only heat rooms you use. 3. Choose tile or stone floors because they move heat better. 4. Seal air leaks around floor joists and edges to stop cold drafts.
Tip: Covering the whole subfloor with insulation lowers your bills and makes your home feel better.
Moisture Control
Moisture can hurt your subfloor insulation and make it work worse. Always look for wet spots before you start. Let the subfloor dry all the way. Put a vapor barrier under the insulation to block water from the ground. If you see water keeps coming back, use a moisture control system. Test for moisture before and while you install to keep insulation dry.
Pick insulation that fits your climate and floor type.
Do not use two vapor barriers because this can trap water.
Seal the floor assembly to keep moist air out.
Note: Controlling moisture keeps your insulation safe and helps you save energy for a long time.
Snug Fit
A tight fit is very important for subfloor insulation. Cut boards so they fit together with no spaces. Stagger the boards like bricks so seams do not line up. Use glue and fasteners to hold boards in place and stop them from moving. Fill small spaces with offcuts or spray foam. Check as you go to keep boards flat and even.
Step | Why It Matters |
---|---|
Stagger seams | Stops heat loss and thermal bridging |
Cut boards precisely | Prevents air gaps |
Secure boards well | Stops shifting and keeps insulation strong |
Callout: A tight fit gives you better insulation, less heat loss, and lower bills.
Common Mistakes
When you work on subfloor insulation, you want to avoid common mistakes that can hurt your results. These errors can lead to wasted money, energy loss, and even damage to your home. Here are the top mistakes you should watch out for:
Skipping Vapor Barrier
If you skip the vapor barrier during subfloor insulation, you risk serious moisture problems. Moisture can move up from the ground or come from humid air. Without a vapor barrier, water can get trapped under your floor. This can cause warping, mold, and even rot in your subfloor. In places with high humidity or basements, this mistake is even more dangerous. You might see your flooring bubble, buckle, or smell musty odors. Always install a vapor barrier to keep your subfloor insulation dry and your floors safe.
Tip: A vapor barrier protects your investment and keeps your home healthy.
Wrong Insulation Thickness
Choosing the wrong thickness for subfloor insulation is a common error. If you use insulation that is too thin, your floor will feel cold, and you will lose heat. If you use insulation that is too thick, you might have trouble with floor height and fitting doors. Some people also use the wrong type, like fiberglass batts, which can fall out or get compressed. This lowers the R-value and makes your insulation less effective. Always check the recommended thickness for your climate and floor type.
Mistake | What Happens Next? |
---|---|
Cold floors, higher energy bills | |
Too thick insulation | Floor height problems, door issues |
Wrong material (e.g., fiberglass batts) | Insulation falls out, poor performance |
Poor Sealing
Poor sealing is another big problem in subfloor insulation projects. If you leave gaps or do not seal seams, air can leak in and out. This makes your home drafty and less comfortable. Warm air escapes, and cold air sneaks in, which means you pay more for heating and cooling. Gaps also let in moisture and even pests. You should use caulk, spray foam, or special tape to seal every seam and opening. Pay close attention to spots where pipes or wires go through the floor.
Callout: Good sealing keeps your subfloor insulation working well and helps stop bugs and mold.
Many people make these mistakes during subfloor insulation: skipping the vapor barrier, using the wrong thickness, or not sealing well. These errors can cause uneven floors, drafts, mold, and high energy bills. Take your time and follow each step to get the best results from your subfloor insulation.
If you follow all the steps for subfloor insulation, your home will feel better and use less energy. Pick good materials, seal every seam, and keep out moisture to protect your house. When you insulate the right way, your floors feel warmer, your bills go down, and you save energy for a long time. Insulation also makes your home worth more and keeps it cozy in every season.
Benefit | Result |
---|---|
Improved comfort | Warmer, draft-free floors |
Energy savings | |
Value |
Remember: Using the right insulation helps your home stay comfortable and saves energy for many years.
FAQ
How thick should floor insulation be?
You should use insulation that matches your climate zone. Most homes need 1 to 2 inches of rigid foam. Check local codes for the best thickness. Thicker insulation gives better warmth but may raise your floor height.
Can you install new flooring directly over insulation?
You should always add an underlayment over the insulation before installing your final flooring. The underlayment protects the insulation, reduces noise, and makes the floor feel smoother underfoot.
Do you need a vapor barrier under every floor?
You need a vapor barrier if your subfloor sits above a crawl space, basement, or concrete slab. The barrier stops moisture from damaging your insulation and flooring. Dry, upper floors may not need one.
What is the best way to cut rigid foam boards?
Use a sharp utility knife for thin boards. For thick boards, use a fine-tooth saw. Always measure twice and cut along a straightedge for clean, tight edges.
Will insulating the floor make your room warmer?
Yes! Insulating your floor keeps heat inside your room. You will feel less cold from the floor, and your heating system will not work as hard. This saves energy and money.