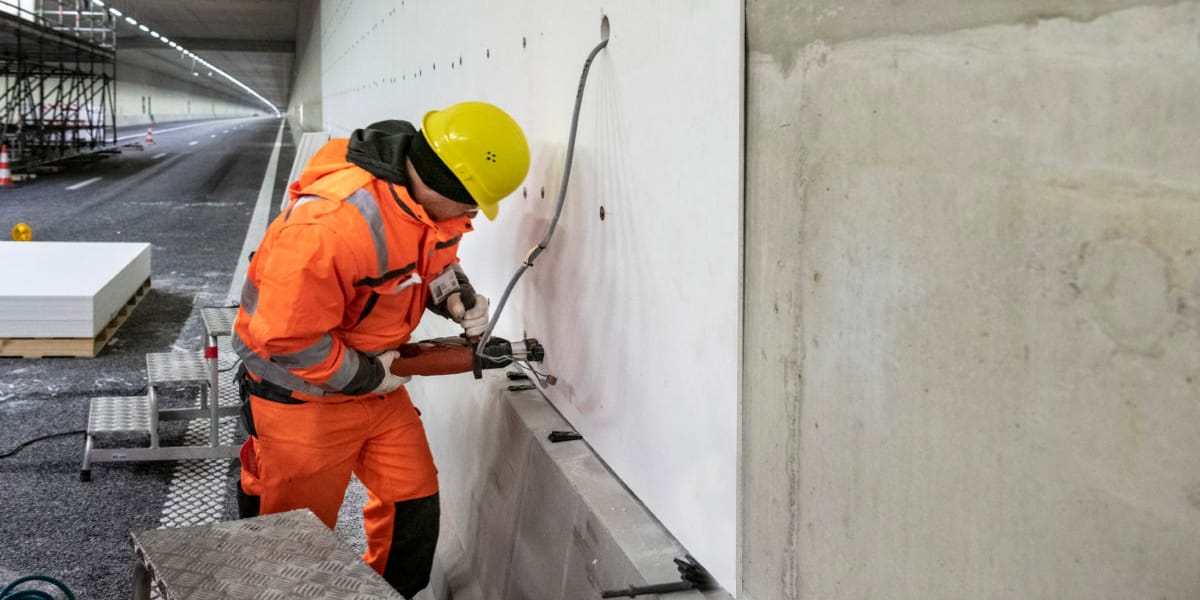
05 Apr Magnesium Oxide Board Wall Sheathing Vs Calcium Silicate Board Wall Sheathing
Table of Contents
When choosing materials for wall sheathing, understanding the differences between magnesium oxide board and calcium silicate board is essential. These materials vary in composition, performance, and suitability for specific applications. For instance, magnesium oxide board, made primarily from magnesium oxide, offers superior fire resistance, higher impact resistance, and greater flexibility. On the other hand, calcium silicate board, composed mainly of calcium silicate, excels in thermal insulation and provides reliable water resistance.
Attribute | MgO Board | Calcium Silicate Board |
---|---|---|
Material Composition | Primarily magnesium oxide | Mainly calcium silicate |
Fire Resistance | Superior | Good |
Water Resistance | More water-resistant | Water-resistant |
Impact Resistance | Higher | Moderate |
Flexibility | More flexible | Less flexible |
Thermal Conductivity | Relatively low | Low, better for insulation |
Ease of Installation | Easier due to lighter weight | Standard installation |
Environmental Impact | More environmentally friendly | Eco-friendly |
Selecting the right material depends on your project’s needs. For example, if you prioritize fire resistance and flexibility, magnesium oxide board might be the better choice. However, for enhanced thermal insulation, calcium silicate board could be more suitable. By understanding these differences, you can make informed decisions that align with your construction goals.
Key Takeaways
Magnesium oxide board is great for fire safety and strong walls.
Calcium silicate board keeps heat in, saving energy in buildings.
Pick the right board for your project needs. MgO board resists water, while calcium silicate board keeps spaces warm.
Both are good for the environment, but MgO board uses less carbon and traps CO₂ when made.
Think about costs over time. MgO board costs more at first but lasts longer and needs less fixing.
Material Composition and Properties
Magnesium Oxide Board (MgO Board)
Composition and Manufacturing
Magnesium oxide board, commonly referred to as MgO board, is made from a combination of materials that contribute to its unique properties. The primary ingredient, magnesium oxide (MgO), ensures excellent fire resistance and strength. Other components include magnesium chloride (MgCl2), which acts as a binder, and perlite, a lightweight volcanic glass that enhances insulation. Wood fiber adds flexibility and strength, while vermiculite expands under heat, providing additional benefits. Glass mesh reinforces the board, making it more durable.
Component | Role/Property Description |
---|---|
Magnesium Oxide (MgO) | Primary ingredient, crucial for fire resistance and strength. |
Magnesium Chloride (MgCl2) | Acts as a binder, ensuring integrity through chemical reaction. |
Perlite | Enhances insulation due to its lightweight volcanic glass nature. |
Wood Fiber | Increases strength and flexibility of the board. |
Vermiculite | Expands when heated, adding unique properties. |
Glass Mesh | Provides additional strength to the MgO boards. |
Key Properties
MgO board is lightweight, with a density ranging from 0.85 to 1.2 g/cm³. It offers high compressive and flexural strength, making it suitable for demanding applications. Its excellent fire resistance and moisture resistance make it a reliable choice for construction. Additionally, the board’s rigidity ensures stability, while its thermal insulation properties contribute to energy efficiency.
Calcium Silicate Board
Composition and Manufacturing
Calcium silicate board is produced through a meticulous process involving pulping, molding, and curing under high temperature and pressure in saturated steam. The calcium source, typically lime, reacts with silica sources like diatomaceous earth or quartz powder. This hydrothermal reaction forms a calcium silicate colloid, which solidifies into durable boards.
Siliceous Materials: Diatomite, quartz sand, and silica fume.
Calcareous Materials: Lime with at least 85% effective CaO content.
Reinforcing Fibers: Alkali-free glass fibers and organic fibers like pulp.
Additives: Sodium silicate and polyacrylamide.
Key Properties
Calcium silicate board has a higher density of 2.92 g/cm³, making it heavier than MgO board. It withstands over 100 pounds of pressure per square inch, showcasing its strength. The board provides good fire resistance and excellent thermal insulation. Its flexibility allows it to adapt to various applications, while its water resistance ensures durability in moist environments.
Comparison of Properties
Strength and Durability
MgO board exhibits high compressive and flexural strength, making it ideal for structural applications. Calcium silicate board, while slightly less strong, can still endure significant pressure and is highly durable.
Resistance to Wear and Tear
MgO board resists wear and tear effectively due to its rigidity and composition. Calcium silicate board, with its flexibility, performs well in environments requiring adaptability but may not match the impact resistance of MgO board.

Performance
Fire Resistance
Magnesium Oxide Board Performance
Magnesium oxide board offers excellent fire resistance due to its inorganic composition. It withstands high temperatures without burning or losing structural integrity. This makes it ideal for fire-rated applications. Unlike other materials, it does not emit toxic fumes when exposed to heat, ensuring safety in fire-prone environments. MgO board can endure up to four hours of fire exposure, maintaining its structure and providing reliable protection.
Material | Fire Resistance Rating | Combustibility | Smoke Emission |
---|---|---|---|
MgO Board | Up to 4 hours | Non-combustible | Minimal |
Particle Board | Less than 1 hour | Highly combustible | Significant |
Calcium Silicate Board Performance
Calcium silicate board also demonstrates good fire resistance, often exceeding two hours in fire-rated scenarios. It achieves a Class A rating for its ability to withstand high temperatures without significant structural damage. However, it begins to crack at 450°C, with severe cracking and failure occurring at 750°C. While it performs well in moderate fire conditions, it may not match the durability of MgO board in extreme heat.
Both materials are non-combustible.
Magnesium oxide board is often cited as having superior fire resistance compared to calcium silicate board.
Moisture Resistance
Performance of MgO Board
MgO board excels in moisture resistance, making it suitable for damp environments. Its composition prevents water absorption, ensuring durability and stability over time. This superior water resistance makes it a preferred choice for areas prone to humidity or water exposure.
Performance of Calcium Silicate Board
Calcium silicate board also resists moisture effectively. It performs well in damp areas, maintaining its structural integrity. However, it is frequently regarded as less water-resistant than magnesium oxide board. For projects requiring maximum moisture protection, MgO board may offer better performance.
Thermal Insulation
Insulation Properties of MgO Board
MgO board has low thermal conductivity, contributing to its insulation properties. While it provides adequate thermal resistance, it may not insulate as effectively as calcium silicate board.
Insulation Properties of Calcium Silicate Board
Calcium silicate board is known for its low thermal conductivity, making it highly effective for insulation. Its ability to retain heat makes it a reliable choice for energy-efficient construction.
Calcium silicate board has low thermal conductivity, making it effective for insulation.
Magnesium oxide board also has low thermal conductivity but may not perform as well in insulation compared to calcium silicate board.
Applications
Uses of Magnesium Oxide Board
Residential Applications
You can use magnesium oxide board (commonly called MgO board) in various residential projects due to its versatility and durability. It works well for both exterior and interior applications. For exteriors, it serves as wall sheathing, fascia, soffit, trim, and lap siding. Indoors, you can rely on it for wall panels, ceiling boards, tile backers, and drop ceiling tiles. It is also an excellent choice for fire wall systems, offering superior fire resistance. Additionally, MgO board is often used in specialty applications like office cubicles, room dividers, and structural insulated panels (SIPs).
Application Type | Examples |
---|---|
Exterior Applications | Wall sheathing, Fascia, Soffit, Trim, Lap Siding |
Interior Applications | Wall panels, Ceiling board, Tile backer, Drop ceiling tiles, Fire wall system |
Specialty Applications | Office cubicles, Room dividers, SIPs |
Commercial and Industrial Applications
In commercial and industrial settings, MgO board excels in areas requiring fire resistance and moisture protection. It is commonly used for fire-rated walls, ceilings, and partitions. Its lightweight nature makes installation easier, reducing labor costs. You’ll also find it in industrial facilities where impact resistance and durability are critical.
Uses of Calcium Silicate Board
Residential Applications
Calcium silicate board is a reliable material for residential construction. You can use it for insulation, fire protection, wall cladding, partitions, flooring, and ceilings. Its water resistance makes it suitable for high-humidity areas like bathrooms and kitchens.
Commercial and Industrial Applications
In commercial spaces, calcium silicate board is widely used in HVAC systems and ductwork. It is also a popular choice for office buildings and fire-rated systems. Industrial applications include thermal insulation to reduce heat transfer and fireproofing to protect structural materials from fire damage.
Wall and Ceiling Panels: Ideal for high-humidity areas.
Insulation: Reduces heat transfer in industrial settings.
Fireproofing: Shields structural materials from fire effects.
Comparison of Applications
Suitability for Different Environments
MgO board performs better in environments requiring high fire resistance and impact durability. It is also more water-resistant, making it ideal for damp or humid conditions. Calcium silicate board, on the other hand, excels in thermal insulation and is a great choice for areas needing heat retention.
Property | Magnesium Oxide Board (MgO) | Calcium Silicate Board |
---|---|---|
Fire Resistance | Superior | Excellent |
Water Resistance | More water-resistant | Water-resistant |
Impact Resistance | Higher impact resistance | Moderate impact resistance |
Flexibility | More flexible | Less flexible |
Thermal Conductivity | Relatively low | Low |
Versatility in Construction
You’ll find both materials versatile, but their strengths differ. MgO board is better for projects requiring lightweight, flexible, and fire-resistant materials. Calcium silicate board is more suitable for applications focused on insulation and fireproofing in industrial and commercial environments.
Cost and Availability
Cost of Magnesium Oxide Board
Price Factors
The cost of MgO board depends on several factors. Its composition, which includes magnesium oxide, perlite, and vermiculite, contributes to its higher price. The manufacturing process, which ensures high durability and moisture-resistant properties, also adds to the cost. However, the board’s impact resistance and ease of installation make it a worthwhile investment for many construction projects. You may find that the price varies based on the board’s thickness, size, and additional features like reinforced glass mesh.
Market Availability
MgO board is widely available in most markets. Its growing popularity stems from its versatility and performance in both residential and commercial applications. You can source it from local suppliers or online retailers, though availability may vary depending on your region. In areas with high demand for fire-resistant and moisture-resistant materials, MgO board is often stocked in abundance.
Cost of Calcium Silicate Board
Price Factors
Calcium silicate board is generally more affordable upfront compared to MgO board. However, its cost is influenced by high production expenses. The manufacturing process involves hydrothermal reactions and the use of raw materials like lime and silica, which can fluctuate in price. Additionally, strict regulations regarding hazardous material handling can increase production costs. These factors make calcium silicate board less competitive in price-sensitive markets.
Market Availability
You can find calcium silicate board in most construction supply stores. Its availability depends on regional demand and the presence of manufacturers. In markets where thermal insulation and fireproofing are priorities, this board is a common choice. However, limited access to raw materials in some areas may affect its supply.
Cost-Effectiveness
Long-Term Value
MgO board offers excellent long-term value. Its durability and minimal maintenance requirements reduce repair and replacement costs. The board’s impact resistance and moisture-resistant properties ensure it performs well over time, making it a cost-effective choice despite its higher initial price.
MgO board requires fewer repairs due to its high durability.
Its moisture-resistant nature prevents damage in damp environments.
Long-term savings outweigh the upfront investment.
Initial Investment
Calcium silicate board has a lower initial cost, making it an attractive option for budget-conscious projects. Its durability and resistance to environmental factors also contribute to reduced maintenance expenses. Additionally, its fire safety compliance can lower insurance costs. However, it may not match the long-term cost-effectiveness of MgO board in certain applications.
Construction costs can decrease by up to 25% with calcium silicate board.
Panels maintain over 70% of their strength after saturation, reducing replacements.
Energy costs may drop significantly due to its insulation properties.

Environmental Impact
Sustainability of Magnesium Oxide Board
Eco-Friendly Practices
Magnesium oxide board stands out for its eco-friendly manufacturing process. It uses non-toxic materials like natural magnesium sulfate, avoiding harmful substances such as benzene and asbestos. The production process consumes less energy, reducing its carbon footprint. During curing, MgO board actively captures CO₂, further contributing to sustainability efforts.
Benefit | Description |
---|---|
Non-toxic materials | Made from natural magnesium sulfate, free from harmful substances. |
Indoor air quality | Produces negligible toxic off-gassing, ensuring safer indoor environments. |
Low-energy manufacturing | Reduces carbon footprint, supporting sustainability efforts. |
CO₂ sequestration | Actively cuts greenhouse gas emissions during the curing process. |
Durability | Resistant to fire, mold, and water, minimizing waste from replacements. |
Recyclability and Disposal
You’ll find MgO board completely recyclable. At the end of its life, it can be repurposed as ground cover or road base material. Leftover material can even serve as a soil nutrient. If recycling isn’t an option, MgO board can be safely disposed of in landfills due to its non-toxic composition.
Recyclable and classified as “Nutritional Waste”.
Magnesium content can be extracted and reused.
Landfill-friendly with no harmful emissions.
Sustainability of Calcium Silicate Board
Eco-Friendly Practices
Calcium silicate board also supports sustainable construction. It is made from renewable materials like lime and silica. The manufacturing process aligns with environmental standards, ensuring minimal ecological disruption.
Recyclability and Disposal
Calcium silicate board is recyclable, making it a responsible choice for eco-conscious projects. Its cleaner manufacturing process reduces environmental harm. However, it lacks the CO₂ sequestration benefits of MgO board.
Made from sustainable materials.
Recyclable, adhering to green building practices.
Environmental Comparison
Carbon Footprint
Magnesium oxide board has a lower carbon footprint compared to calcium silicate board. Its production emits less CO₂ and even captures greenhouse gases during curing. Both materials are eco-friendly, but MgO board’s ability to sequester CO₂ gives it an edge.
MgO board: Lower CO₂ emissions, CO₂ sequestration during curing.
Calcium silicate board: Higher CO₂ emissions but still eco-friendly.
Resource Efficiency
MgO board demonstrates better resource efficiency due to its lightweight nature and lower environmental impact. Calcium silicate board, while durable, requires more energy-intensive production.
Feature | Magnesium Oxide Board | Calcium Silicate Board |
---|---|---|
Environmental Impact | Lower CO₂ emissions | Higher CO₂ emissions |
Recyclability | Completely recyclable | Recyclable |
Resource Efficiency | High | Moderate |
When deciding between magnesium oxide board and calcium silicate board, you should consider their unique strengths. MgO board offers superior fire resistance, impact durability, and water resistance, making it ideal for damp environments or fire-rated applications. However, it has lower thermal insulation compared to calcium silicate board. Calcium silicate board excels in thermal insulation, fireproofing, and durability, especially in high-temperature or high-traffic areas. For projects prioritizing moisture resistance and longevity, MgO board is a strong choice. If insulation and fireproofing are critical, calcium silicate board provides excellent performance.